What Types of Materials Are Commonly Used For PCB Conformal Coating Services?
What Types of Materials Are Commonly Used For PCB Conformal Coating Services?
The importance of PCB conformal coating can’t be understated. As a kind of armor for the circuit board, it helps protect the board from dirt, dust, and moisture. Without it, sensors and fragile electronic components are at risk of failure or damage due to temperature fluctuations, chemistry changes or exposure hazards like ultraviolet light.
Conformal coating performs a crucial step in electronics manufacturing – not only is there an elevated level of certainty that comes from this added layer, but its resistance also protects what’s expected, preserving performance despite challenges posed by aircraft engines, automotive components or medical environments.
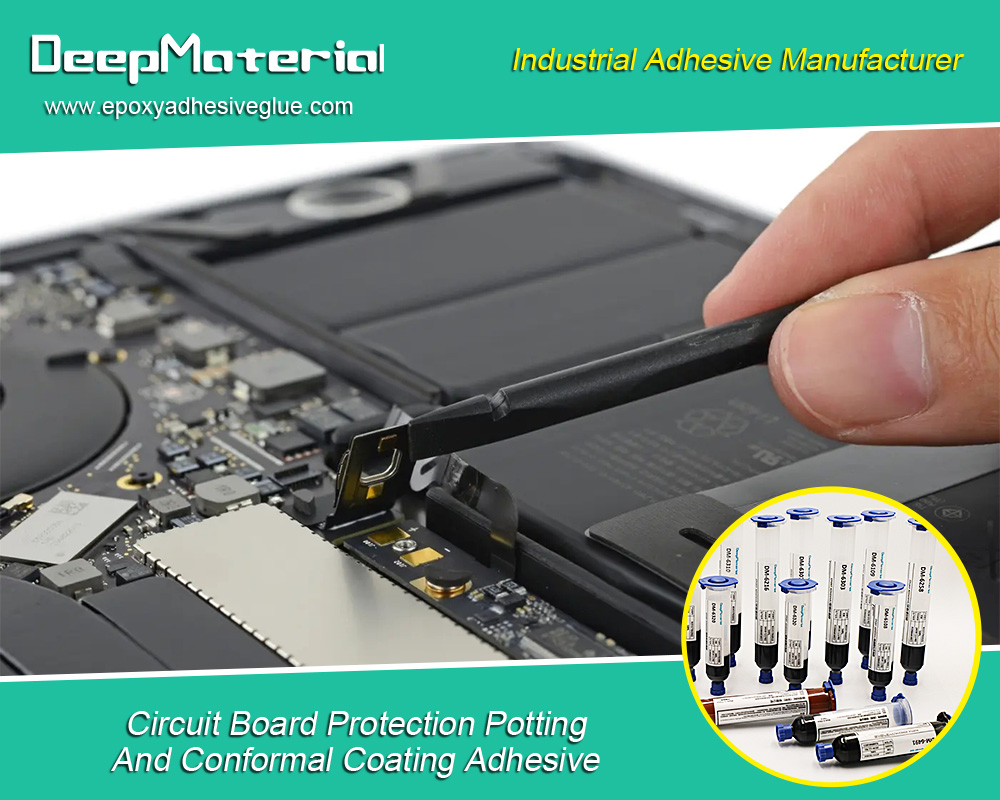
Types of Materials Used for Conformal Coating
With an array of options, deciding which conformal coating material to use comes down to evaluating factors such as the app’s specifications, climate circumstances and stubbornness against physical abuse. Each offers unique perks and benefits that make them stand out from the crowd – So picking one for your app needs some consideration.
Acrylic conformal coating
Acrylic coatings are super versatile and the easiest to apply for protecting components from moisture, chemicals, and temperature changes – not to mention their fantastic insulation abilities. Plus, you can quickly fix it up or take it off if need be. All in all, acrylic coatings are usually a safe bet.
Silicone coatings are a heavy hitter when it comes to protection from moisture and high temps. Boasting extraordinary resistance against chemicals and rays, they’re the ultimate pick for exterior applications; plus, these tough topcoats have stand-up flexibility, so you won’t ever have to worry about them cracking or flaking away.
Urethane conformal coating
Urethane coatings are like a shielding blanket; they guard against wetness, chemical compounds and undue friction. Not only does their insulative quality keep electricity in check, but they can also hold their own to intense heat. Plus, these trusty protectors are immune to fungi growth and stick fast – regardless of the surface – without fail.
Epoxy conformal coating
Epoxy coatings are definitely the savvy choice when it comes to safeguarding against moisture, chemicals, and extreme temperatures. What’s more, they go one step further – they don’t just deliver electrical insulation properties. With epoxies, you get remarkable protection for all surfaces in even the most unrelenting environments. It really packs a punch, too, because epoxy coatings provide a robust defence against fungi as well as sticking to virtually any substrate like glue.
Parylene conformal coating
Out of this world, that’s what Parylene coatings are! This unique vapor-solid entropy forms an incredibly thin and transparent film. Not only does it protect from moisture, chemicals, and temperature fluctuations – but it ensures respectable electrical insulation, too. It’s definitely the ace in tricky situations, particularly when you need a lightweight coating yet still want excellent protection.
Comparison of Different Types of Conformal Coatings
Each version of conformal coating offers its pros and cons, making them apt for distinct applications.
The acrylic conformable coating has the advantage of being multifunctional and easy to apply, in addition to offering top-notch shelter from moisture and chemicals with some stellar electrical insulation properties.
Unfortunately, however, it only harbors lackluster resistance to high temperatures that may further cause yellowing or discoloring over time. On the contrary, silicone conformal coating provides outstanding protection when it comes to guarding against humidity & extreme temperatures, along with having excellent durability versus chemicals & UV radiation – though removing/repairing this kind may be pretty tricky without exclusive equipment application needed.
Meanwhile, urethane coatings stave off moisture while also protecting splendidly against chemical exposure & abrasion. Still, yet again, they don’t quite stand up well under blazing temperature extremes whilst requiring increased curing times.
In comparison, epoxy coatings have robust defence capabilities ranging from safeguarding against water vapor up to repelling chemical aggressors coupled with hardy thermal stability, whereas perylene offers excellent resistance characteristics just like its counterparts as long as there are specialized outfits ready for implementation properly.
Factors to Consider When Choosing a Conformal Coating Material
When choosing a conformal coating material, several factors need to be taken into consideration:
Environmental factors
Considering your PCB’s use environment is critical. Temperature swings, moisture levels, chemical exposure, dust and UV radiation all have the potential to wreak havoc on a board over time – causing malfunction or total failure. Pick a protective coating material carefully!
For example, facing extreme heat? Pick something that can take the heat. Worried about chem/radiation damage? Get something able to repel those baddies. It’s an essential element to ensure successful longevity for your circuit board’s life cycle.
Application method
When it comes to covering circuit boards (PCBs) with protective layers, the method of application is a game-changer – because certain coatings won’t fly with specific methods. For instance, spray applications are generally better for more extensive and intricate PCBs, while dip or brush applications could suffice for simpler ones.
The team has to weigh a few things when choosing an application: size & complexity of the board, desired level of protection – all will affect the kind of coating needed, so spraying might be the way to go on larger projects whilst brushing and dipping work much better for smaller jobs.
Cost
Weighing cost is vital when selecting a conformal coating material. Though some options are pricier, they may come with extra perks that make them worth it. It all depends on the protection you need and the application’s specific requirements.
For example, if you’re looking for utmost resistance to hostile chemicals or sweltering temperatures, coughing up more dough could be a wise investment. However, if lower-level security suffices for your situation, an affordable option should do just fine in getting the job done.
Compatibility with other materials
Making the right coating material selection for a PCB assembly is nothing short of essential – it must work with everything else used in the process. It should cling effectively to its substrate and not clash with any other materials involved in fabrication.
If you get your selection wrong, you may find yourself stuck between a rock and a hard place: poor adhesion, delamination or even problems with your board that could put it at risk of failing to meet industry standards. To avoid these issues, double-check your compatibility so you can say goodbye to inferior products and hello to quality assurance!
Final Thoughts on PCB Conformal Coating Materials
To sum up, PCB conformal coating is a must-have in any electronics manufacturer. This miraculous procedure shields every Printed Circuit Board from unwelcome environmental agents such as humidity, chemical contaminants, particles of dust and more that constantly threaten their reliability and functioning. Regrettably, it is not an effortless task, for there are many competing types of material available, making selecting one quite complicated.
To make sure you’re choosing the correct solution, it’s imperative to consider factors like ecological constraints (e.g. thermal shock) and the application method desired – all while keeping other stuff in view, such as compatibility with other elements added into consideration, followed by cost-saving being approached too! When you’ve thoughtfully weighed all these variables, consequently picking up your ideal conformal coatings should be a walk in the park — ultimately delivering optimal protection to your cherished boards!
For more about choosing the PCB Conformal Coating Services, you can pay a visit to DeepMaterial at https://www.epoxyadhesiveglue.com/category/epoxy-adhesives-glue/ for more info.