Best underfill epoxy adhesive manufacturer and supplier
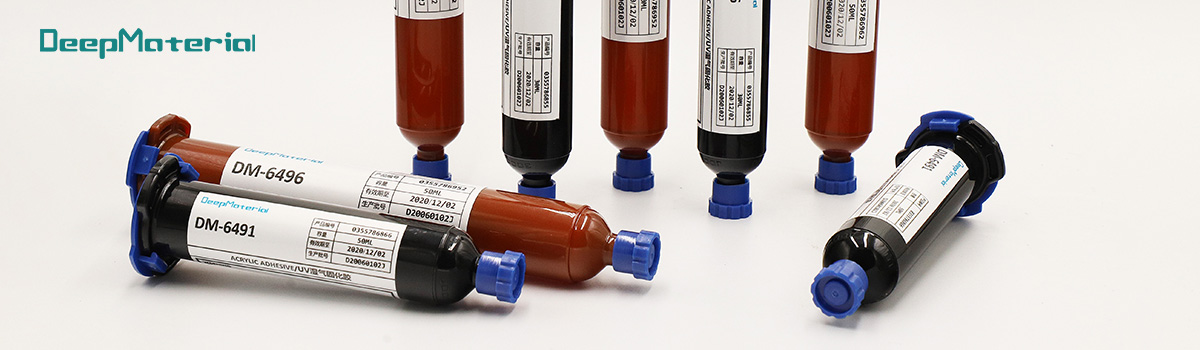
Shenzhen DeepMaterial Technologies Co., Ltd is flip chip bga underfill epoxy material and epoxy encapsulant manufacturer in china,manufacturing underfill encapsulants,smt pcb underfill epoxy,one component epoxy underfill compounds,flip chip underfill epoxy for csp and bga and so on.
Underfill is an epoxy material that fills gaps between a chip and its carrier or a finished package and the PCB substrate. Underfill protects electronic products from shock, drop, and vibration and reduces the strain on fragile solder connections caused by the difference in thermal expansion between the silicon chip and carrier (two unlike materials).
In capillary underfill applications, a precise volume of underfill material is dispensed along the side of a chip or package to flow underneath through capillary action, filling air gaps around solder balls that connect chip packages to the PCB or stacked chips in multi-chip packages. No-flow underfill materials, sometimes used for underfilling, are deposited on the substrate before a chip or package is attached and reflowed. Molded underfill is another approach that involves using resin to fill gaps between the chip and substrate.
Without underfill, the life expectancy of a product would be significantly reduced due to the cracking of interconnects. Underfill is applied at the following stages of the manufacturing process to improve reliability.
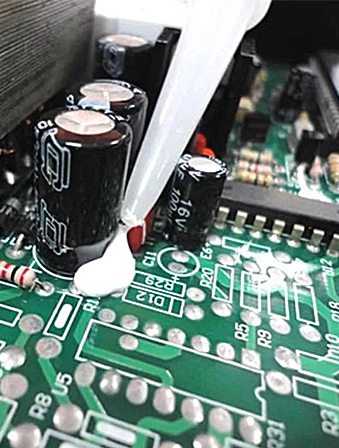
Complete Guide Of Underfill Epoxy :
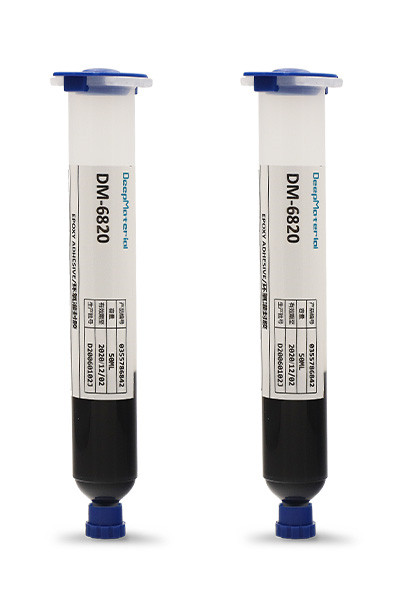
What Is Epoxy Underfill?
Underfill is a type of epoxy material that is used to fill gaps between a semiconductor chip and its carrier or between a finished package and the printed circuit board (PCB) substrate in electronic devices. It is typically used in advanced semiconductor packaging technologies, such as flip-chip and chip-scale packages, to enhance the mechanical and thermal reliability of the devices.
Epoxy underfill is typically made of epoxy resin, a thermosetting polymer with excellent mechanical and chemical properties, making it ideal for use in demanding electronic applications. The epoxy resin is typically combined with other additives, such as hardeners, fillers, and modifiers, to enhance its performance and tailor its properties to meet specific requirements.
Epoxy underfill is a liquid or semi-liquid material dispensed onto the substrate before the semiconductor die is placed on top. It is then cured or solidified, usually through a thermal process, to form a rigid, protective layer that encapsulates the semiconductor die and fills the gap between the die and the substrate.
Epoxy underfill is a specialized adhesive material used in electronics manufacturing to encapsulate and protect delicate components, such as microchips, by filling the gap between the element and the substrate, typically a printed circuit board (PCB). It is commonly used in flip-chip technology, where the chip is mounted face-down on the substrate to improve thermal and electrical performance.
The primary purpose of epoxy underfills is to provide mechanical reinforcement to the flip-chip package, improving its resistance to mechanical stresses such as thermal cycling, mechanical shocks, and vibrations. It also helps to reduce the risk of solder joint failures due to fatigue and thermal expansion mismatches, which can occur during the operation of the electronic device.
Epoxy underfill materials are typically formulated with epoxy resins, curing agents, and fillers to achieve the desired mechanical, thermal, and electrical properties. They are designed to have good adhesion to the semiconductor die and the substrate, a low coefficient of thermal expansion (CTE) to minimize thermal stress, and high thermal conductivity to facilitate heat dissipation from the device.
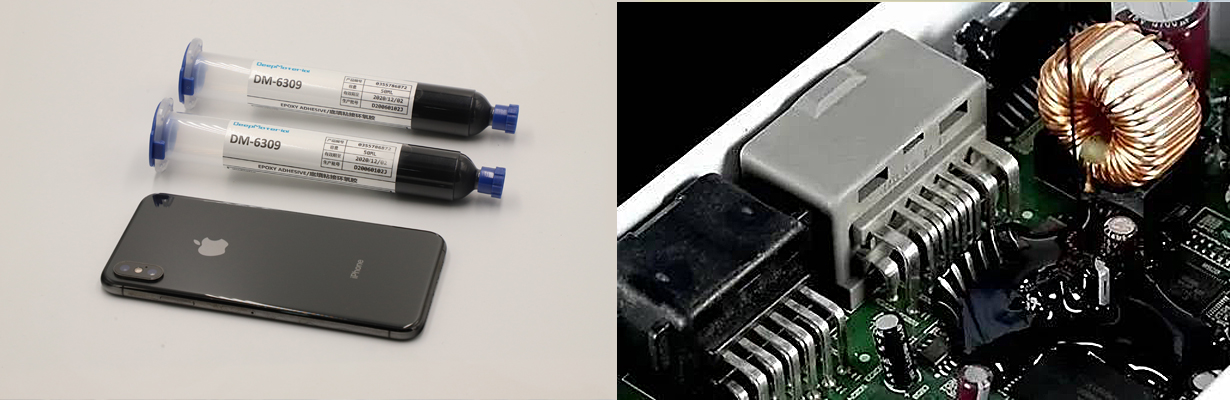
What Is Underfill Epoxy Used For?
Underfill epoxy is an epoxy resin adhesive used in various applications to provide mechanical reinforcement and protection. Here are some common uses of underfill epoxy:
Semiconductor Packaging: Underfill epoxy is commonly used in semiconductor packaging to provide mechanical support and protection to delicate electronic components, such as microchips, mounted on printed circuit boards (PCBs). It fills the gap between the chip and the PCB, preventing stress and mechanical damage caused by thermal expansion and contraction during operation.
Flip-Chip Bonding: Underfill epoxy is used in flip-chip bonding, which connects semiconductor chips directly to a PCB without wire bonds. The epoxy fills the gap between the chip and the PCB, providing mechanical reinforcement and electrical insulation while improving thermal performance.
Display Manufacturing: Underfill epoxy is used to manufacture displays, such as liquid crystal displays (LCDs) and organic light-emitting diode (OLED) shows. It is used to bond and reinforce delicate components, such as display drivers and touch sensors, to ensure mechanical stability and durability.
Optoelectronic Devices: Underfill epoxy is used in optoelectronic devices, such as optical transceivers, lasers, and photodiodes, to provide mechanical support, improve thermal performance, and protect sensitive components from environmental factors.
Automotive Electronics: Underfill epoxy is used in automotive electronics, such as electronic control units (ECUs) and sensors, to provide mechanical reinforcement and protection against temperature extremes, vibrations, and harsh environmental conditions.
Aerospace and Defense Applications: Underfill epoxy is used in aerospace and defense applications, such as avionics, radar systems, and military electronics, to provide mechanical stability, protection against temperature fluctuations, and resistance to shock and vibration.
Consumer Electronics: Underfill epoxy is used in various consumer electronics, including smartphones, tablets, and gaming consoles, to provide mechanical reinforcement and protect electronic components from damage due to thermal cycling, impact, and other stresses.
Medical Devices: Underfill epoxy is used in medical devices, such as implantable devices, diagnostic equipment, and monitoring devices, to provide mechanical reinforcement and protect delicate electronic components from harsh physiological environments.
LED Packaging: Underfill epoxy is used in packaging light-emitting diodes (LEDs) to provide mechanical support, thermal management, and protection against moisture and other environmental factors.
General Electronics: Underfill epoxy is used in a wide range of general electronics applications where mechanical reinforcement and protection of electronic components are required, such as in power electronics, industrial automation, and telecommunications equipment.
What Is Underfill Material For Bga?
Underfill material for BGA (Ball Grid Array) is an epoxy or polymer-based material used to fill the gap between the BGA package and the PCB (Printed Circuit Board) after soldering. BGA is a type of surface mount package used in electronic devices that provides a high density of connections between the integrated circuit (IC) and the PCB. Underfill material enhances BGA solder joints’ reliability and mechanical strength, mitigating the risk of failures due to mechanical stresses, thermal cycling, and other environmental factors.
Underfill material is typically liquid and flows under the BGA package via capillary action. It then undergoes a curing process to solidify and create a rigid connection between the BGA and the PCB, usually through heat or UV exposure. The underfill material helps to distribute mechanical stresses that can occur during thermal cycling, reducing the risk of solder joint cracking and improving the overall reliability of the BGA package.
Underfill material for BGA is carefully selected based on factors such as the specific BGA package design, the materials used in the PCB and the BGA, the operating environment, and the intended application. Some common underfill materials for BGA include epoxy-based, no-flow, and underfills with different filler materials such as silica, alumina, or conductive particles. The selection of the appropriate underfill material is critical to ensure the long-term reliability and performance of BGA packages in electronic devices.
Additionally, underfill material for BGA can provide protection against moisture, dust, and other contaminants that may otherwise penetrate the gap between the BGA and the PCB, potentially causing corrosion or short circuits. This can help enhance BGA packages’ durability and reliability in harsh environments.
What Is Underfill Epoxy In Ic?
Underfill epoxy in IC (Integrated Circuit) is an adhesive material that fills the gap between the semiconductor chip and the substrate (such as a printed circuit board) in electronic devices. It is commonly used in the manufacturing process of ICs to enhance their mechanical strength and reliability.
ICs are typically made up of a semiconductor chip that contains various electronic components, such as transistors, resistors, and capacitors, which are connected to external electrical contacts. These chips are then mounted onto a substrate, which provides support and electrical connectivity to the rest of the electronic system. However, due to differences in coefficients of thermal expansion (CTEs) between the chip and the substrate and the stresses and strains experienced during operation, mechanical stress, and reliability issues can arise, such as thermal cycling-induced failures or mechanical cracks.
Underfill epoxy addresses these issues by filling the gap between the chip and the substrate, creating a mechanically robust bond. It is a type of epoxy resin formulated with specific properties, such as low viscosity, high adhesion strength, and good thermal and mechanical properties. During the manufacturing process, the underfill epoxy is applied in a liquid form, and then it is cured to solidify and create a strong bond between the chip and the substrate. ICs are sensitive electronic devices susceptible to mechanical stress, temperature cycling, and other environmental factors during operation, which can cause failure due to solder joint fatigue or delamination between the chip and the substrate.
The underfill epoxy helps redistribute and minimize the mechanical stresses and strains during operation and provides protection against moisture, contaminants, and mechanical shocks. It also helps to improve the thermal cycling reliability of the IC by reducing the risk of cracking or delamination between the chip and the substrate due to temperature changes.
What Is Underfill Epoxy In Smt?
Underfill epoxy in Surface Mount Technology (SMT) refers to a type of adhesive material used to fill the gap between a semiconductor chip and the substrate in electronic devices such as printed circuit boards (PCBs). SMT is a popular method for assembling electronic components on PCBs, and underfill epoxy is commonly used to improve the mechanical strength and reliability of the solder joints between the chip and the PCB.
When electronic devices are subjected to thermal cycling and mechanical stress, such as during operation or transportation, the differences in coefficient of thermal expansion (CTE) between the chip and the PCB can cause strain on the solder joints, leading to potential failures such as cracks or delamination. Underfill epoxy is used to mitigate these issues by filling the gap between the chip and the substrate, providing mechanical support, and preventing the solder joints from experiencing excessive stress.
Underfill epoxy is typically a thermosetting material dispensed in liquid form onto the PCB, and it flows into the gap between the chip and the substrate through capillary action. It is then cured to form a rigid and durable material that bonds the chip to the substrate, improving the overall mechanical integrity of the solder joints.
Underfill epoxy serves several essential functions in SMT assemblies. It helps to minimize the formation of solder joint cracks or fractures due to thermal cycling and mechanical stresses during the operation of electronic devices. It also enhances the thermal dissipation from the IC to the substrate, which helps to improve the reliability and performance of the electronic assembly.
Underfill epoxy in SMT assemblies requires precise dispensing techniques to ensure proper coverage and uniform distribution of the epoxy without causing any damage to the IC or the substrate. Advanced equipment such as dispensing robots and curing ovens are commonly used in the underfill process to achieve consistent results and high-quality bonds.
What Are The Properties Of Underfill Material?
Underfill materials are commonly used in electronics manufacturing processes, specifically, semiconductor packaging, to enhance the reliability and durability of electronic devices such as integrated circuits (ICs), ball grid arrays (BGAs), and flip-chip packages. The properties of underfill materials can vary depending on the specific type and formulation but generally include the following:
Thermal conductivity: Underfill materials should have good thermal conductivity to dissipate heat generated by the electronic device during operation. This helps prevent overheating, which can lead to devise failure.
CTE (Coefficient of Thermal Expansion) compatibility: Underfill materials should have a CTE that is compatible with the CTE of the electronic device and the substrate it is bonded to. This helps to minimize thermal stress during temperature cycling and prevents delamination or cracking.
Low viscosity: Underfill materials should have a low density to enable them to flow easily during the encapsulation process and fill gaps between the electronic device and the substrate, ensuring uniform coverage and minimizing voids.
Adhesion: Underfill materials should have good adhesion to the electronic device and the substrate to provide a strong bond and prevent delamination or separation under thermal and mechanical stresses.
Electrical insulation: Underfill materials should have high electrical insulation properties to prevent short circuits and other electrical failures in the device.
Mechanical strength: Underfill materials should have the sufficient mechanical strength to withstand the stresses encountered during temperature cycling, shock, vibration, and other mechanical loads without cracking or deforming.
Cure time: Underfill materials should have an appropriate cure time to ensure proper bonding and curing without causing delays in the manufacturing process.
Dispensing and reworkability: Underfill materials should be compatible with the dispensing equipment used in manufacturing and allow for rework or repair if needed.
Moisture resistance: Underfill materials should have good moisture resistance to prevent moisture ingress, which can cause device failure.
Shelf life: Underfill materials should have a reasonable shelf life, allowing for proper storage and usability over time.
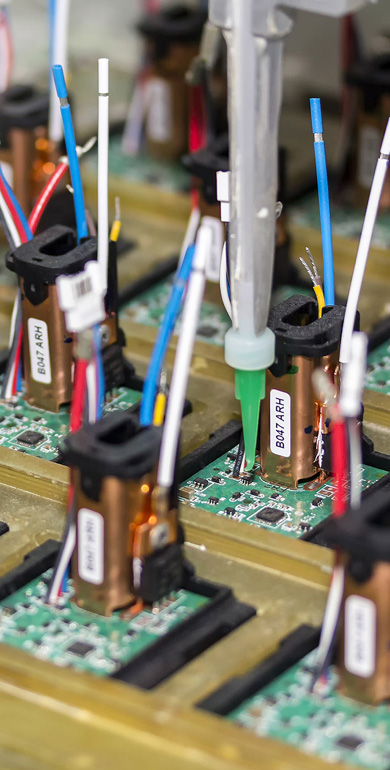
What Is A Molded Underfill Material?
A molded underfill material is used in electronic packaging to encapsulate and protect semiconductor devices, such as integrated circuits (ICs), from external environmental factors and mechanical stresses. It is typically applied as a liquid or paste material and then cured to solidify and create a protective layer around the semiconductor device.
Molded underfill materials are commonly used in flip-chip packaging, which interconnects semiconductor devices to a printed circuit board (PCB) or substrate. Flip-chip packaging allows for a high-density, high-performance interconnect scheme, where the semiconductor device is mounted face-down on the substrate or PCB, and the electrical connections are made using metal bumps or solder balls.
The molded underfill material is typically dispensed in a liquid or paste form and flows under the semiconductor device by capillary action, filling the gaps between the device and the substrate or PCB. The material is then cured using heat or other curing methods to solidify and create a protective layer that encapsulates the device, providing mechanical support, thermal insulation, and protection against moisture, dust, and other contaminants.
Molded underfill materials are typically formulated to have properties such as low viscosity for easy dispensing, high thermal stability for reliable performance in a wide range of operating temperatures, good adhesion to different substrates, low coefficient of thermal expansion (CTE) to minimize stress during temperature cycling, and high electrical insulation properties to prevent short circuits.
Certainly! In addition to the properties mentioned earlier, molded underfill materials may have other characteristics tailored to specific applications or requirements. For example, some developed underfill materials may have enhanced thermal conductivity to improve heat dissipation from the semiconductor device, which is essential in high-power applications where thermal management is critical.
How Do You Remove Underfill Material?
Removing underfilled material can be challenging, as it is designed to be durable and resistant to environmental factors. However, several standard methods can be used to remove underfill material, depending on the specific type of underfill and the desired outcome. Here are some options:
Thermal methods: Underfill materials are typically designed to be thermally stable, but they can sometimes be softened or melted by applying heat. This can be done using specialized equipment such as a hot air rework station, a soldering iron with a heated blade, or an infrared heater. The softened or melted underfill can then be carefully scraped or lifted away using a suitable tool, such as a plastic or metal scraper.
Chemical methods: Chemical solvents can dissolve or soften some underfilled materials. The type of solvent needed depends on the specific type of underfill material. Typical solvents for underfill removal include isopropyl alcohol (IPA), acetone, or specialized underfill removal solutions. The solvent is typically applied to the underfill material and allowed to penetrate and soften it, after which the material can be carefully scraped or wiped away.
Mechanical methods: Underfill material can be removed mechanically using abrasive or mechanical methods. This can include techniques such as grinding, sanding, or milling, using specialized tools or equipment. Automated processes are typically more aggressive and may be suitable for cases where other ways are not effective, but they can also pose risks of damaging the underlying substrate or components and should be used with caution.
Combination methods: In some cases, a combination of techniques may remove underfilled material. For example, various thermal and chemical processes may be used, where heat is applied to soften the underfill material, solvents to further dissolve or soften the material, and mechanical methods to remove the remaining residue.
How To Fill Underfill Epoxy
Here’s a step-by-step guide on how to underfill epoxy:
Step 1: Gather Materials and Equipment
Underfill epoxy material: Choose a high-quality underfill epoxy material that is compatible with the electronic components you are working with. Follow the manufacturer’s instructions for mixing and curing times.
Dispensing equipment: You will need a dispensing system, such as a syringe or a dispenser, to apply the epoxy accurately and uniformly.
Heat source (optional): Some underfilled epoxy materials require curing with heat, so you may need a heat source, such as an oven or a hot plate.
Cleaning materials: Have isopropyl alcohol or a similar cleaning agent, lint-free wipes, and gloves for cleaning and handling the epoxy.
Step 2: Prepare the Components
Clean the components: Ensure that the components to be underfilled are clean and free from any contaminants, such as dust, grease, or moisture. Clean them thoroughly using isopropyl alcohol or a similar cleaning agent.
Apply adhesive or flux (if needed): Depending on the underfill epoxy material and the components being used, you may need to apply an adhesive or flux to the components before applying the epoxy. Follow the manufacturer’s instructions for the specific material being used.
Step 3: Mix the Epoxy
Follow the manufacturer’s instructions to mix the underfill epoxy material properly. This may involve combining two or more epoxy components in specific ratios and stirring them thoroughly to achieve a homogeneous mixture. Use a clean and dry container for mixing.
Step 4: Apply the Epoxy
Load the epoxy into the dispensing system: Fill the dispensing system, such as a syringe or a dispenser, with the mixed epoxy material.
Apply the epoxy: Dispense the epoxy material onto the area that needs to be underfilled. Be sure to apply the epoxy in a uniform and controlled manner to ensure complete coverage of the components.
Avoid air bubbles: Avoid trapping air bubbles in the epoxy, as they can affect the performance and reliability of the underfilled components. Use proper dispensing techniques, such as slow and steady pressure, and gently eliminate any trapped air bubbles with a vacuum or tap the assembly.
Step 5: Cure the Epoxy
Cure the epoxy: Follow the manufacturer’s instructions for curing the underfill epoxy. Depending on the epoxy material used, this may involve fixing at room temperature or using a heat source.
Allow for proper curing time: Give the epoxy sufficient time to cure fully before handling or further processing the components. Depending on the epoxy material and curing conditions, this may take several hours to a few days.
Step 6: Clean and Inspect
Clean the excess epoxy: Once the epoxy has cured, remove any excess epoxy using appropriate cleaning methods, such as scraping or cutting.
Inspect the underfilled components: Inspect the underfilled components for any defects, such as voids, delamination, or incomplete coverage. If any defects are found, take appropriate corrective measures, such as re-filling or re-curing, as needed.
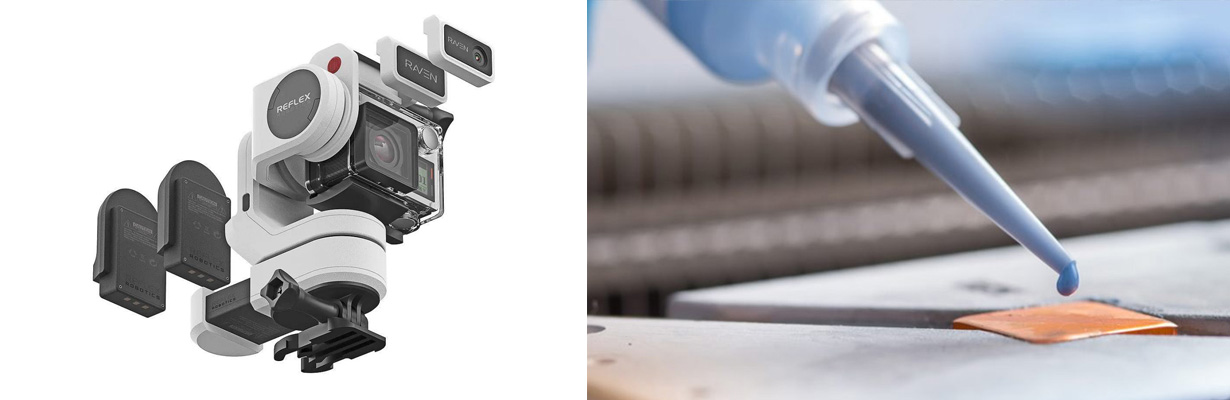
When Do You Fill Underfill Epoxy
The timing of underfill epoxy application will depend on the specific process and application. Underfill epoxy is generally applied after the microchip has been mounted onto the circuit board and the solder joints have been formed. Using a dispenser or syringe, the underfill epoxy is then dispensed in a small gap between the microchip and the circuit board. The epoxy is then cured or hardened, typically heating it to a specific temperature.
The exact timing of the underfill epoxy application may depend on factors such as the type of epoxy used, the size and geometry of the gap to be filled, and the specific curing process. Following the manufacturer’s instructions and recommended method for the particular epoxy being used is essential.
Here are some everyday situations when underfill epoxy may be applied:
Flip-chip bonding: Underfill epoxy is commonly used in flip-chip bonding, a method of attaching a semiconductor chip directly to a PCB without wire bonding. After the flip-chip is attached to the PCB, underfill epoxy is typically applied to fill the gap between the chip and the PCB, providing mechanical reinforcement and protecting the chip from environmental factors such as moisture and temperature changes.
Surface mount technology (SMT): Underfill epoxy may also be used in surface mount technology (SMT) processes, where electronic components such as integrated circuits (ICs) and resistors are mounted directly onto the surface of a PCB. Underfill epoxy may be applied to reinforce and protect these components after being sold onto the PCB.
Chip-on-board (COB) assembly: In chip-on-board (COB) assembly, bare semiconductor chips are attached directly to a PCB using conductive adhesives, and underfill epoxy may be used to encapsulate and reinforce the chips, improving their mechanical stability and reliability.
Component-level repair: Underfill epoxy may also be used in component-level repair processes, where damaged or faulty electronic components on a PCB are replaced with new ones. Underfill epoxy may be applied to the replacement component to ensure proper adhesion and mechanical stability.
Is Epoxy Filler Waterproof
Yes, the epoxy filler is generally waterproof once it has healed. Epoxy fillers are known for their excellent adhesion and water resistance, making them a popular choice for a variety of applications that require a robust and waterproof bond.
When used as a filler, epoxy can effectively fill cracks and gaps in various materials, including wood, metal, and concrete. Once cured, it creates a hard, durable surface resistant to water and moisture, making it ideal for use in areas exposed to water or high humidity.
However, it’s important to note that not all epoxy fillers are created equal, and some may have different levels of water resistance. It’s always a good idea to check the specific product’s label or consult the manufacturer to ensure it’s suitable for your project and intended use.
To ensure the best results, it is essential to properly prepare the surface before applying the epoxy filler. This typically involves cleaning the area thoroughly and removing any loose or damaged material. Once the surface is prepared correctly, the epoxy filler can be mixed and applied according to the manufacturer’s instructions.
It is also important to note that not all epoxy fillers are created equal. Some products may be more suited for specific applications or surfaces than others, so choosing the right product for the job is essential. Additionally, some epoxy fillers may require additional coatings or sealers to provide long-lasting waterproofing protection.
Epoxy fillers are famous for their waterproofing properties and ability to create a robust and durable bond. However, following proper application techniques and choosing the right product are essential to ensure the best results.
Underfill Epoxy Flip Chip Process
Here are the steps to perform an underfill epoxy flip chip process:
Cleaning: The substrate and the flip chip are cleaned to remove any dust, debris, or contaminants that could interfere with the underfilled epoxy bond.
Dispensing: The underfilled epoxy is dispensed onto the substrate in a controlled manner, using a dispenser or a needle. The dispensing process must be precise to avoid any overflow or voids.
Alignment: The flip chip is then aligned with the substrate using a microscope to ensure accurate placement.
Reflow: The flip chip is reflowed using a furnace or an oven to melt the solder bumps and bond the chip to the substrate.
Curing: The underfilled epoxy is cured by heating it in an oven at a specific temperature and time. The curing process allows the epoxy to flow and fill any gaps between the flip chip and the substrate.
Cleaning: After the curing process, any excess epoxy is removed from the edges of the chip and substrate.
Inspection: The final step is to inspect the flip chip under a microscope to ensure no voids or gaps in the underfilled epoxy.
Post-cure: In some cases, a post-cure process may be necessary to improve the mechanical and thermal properties of the underfilled epoxy. This involves heating the chip again at a higher temperature for a more extended period to achieve a more complete cross-linking of the epoxy.
Electrical testing: After the underfill epoxy flip-chip process, the device is tested to ensure it functions properly. This may involve checking for shorts or opens in the circuit and testing the electrical characteristics of the device.
Packaging: Once the device has been tested and verified, it can be packaged and shipped to the customer. The packaging may involve additional protection, such as a protective coating or encapsulation, to ensure the device is not damaged during transportation or handling.
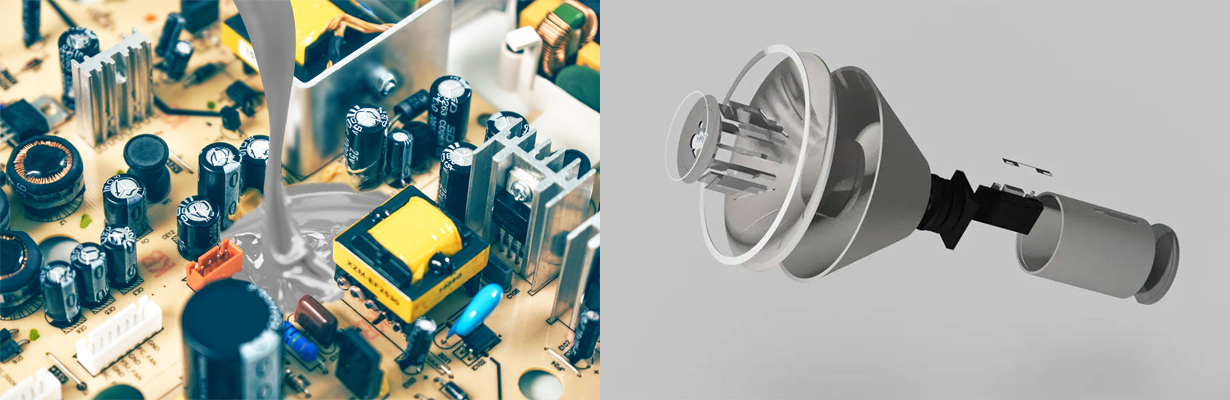
Epoxy Underfill Bga Method
The process involves filling the space between the BGA chip and the circuit board with epoxy, which provides additional mechanical support and improves the thermal performance of the connection. Here are the steps involved in the epoxy underfill BGA method:
- Prepare the BGA package and PCB by cleaning them with a solvent to remove contaminants that may affect the bond.
- Apply a small amount of flux to the center of the BGA package.
- Place the BGA package onto the PCB and use a reflow oven to solder the package onto the board.
- Apply a small amount of epoxy underfill to the corner of the BGA package. The underfill should be applied to the corner closest to the center of the package, and should not cover any of the solder balls.
- Use a capillary action or vacuum to draw the underfill under the BGA package. The underfill should flow around the solder balls, filling any voids and creating a solid bond between the BGA and PCB.
- Cure the underfill according to the manufacturer’s instructions. This usually involves heating the assembly to a specific temperature for a specific amount of time.
- Clean the assembly with a solvent to remove any excess flux or underfill.
- Inspect the underfill for voids, bubbles, or other defects that may compromise the performance of the BGA chip.
- Clean any excess epoxy from the BGA chip and circuit board using a solvent.
- Test the BGA chip to ensure that it is functioning correctly.
Epoxy underfill provides a number of benefits for BGA packages, including improved mechanical strength, reduced stress on the solder joints, and increased resistance to thermal cycling. However, following the manufacturer’s instructions carefully ensures a robust and reliable bond between the BGA package and PCB.
How To Make Underfill Epoxy Resin
Underfill epoxy resin is a type of adhesive used to fill gaps and strengthen electronic components. Here are the general steps for making underfilled epoxy resin:
- Ingredients:
- Epoxy resin
- Hardener
- Filler materials (such as silica or glass beads)
- Solvents (such as acetone or isopropyl alcohol)
- Catalysts (optional)
Steps:
Choose the suitable epoxy resin: Select an epoxy resin that is suitable for your application. Epoxy resins come in a variety of types with varying properties. For underfill applications, choose a resin with high strength, low shrinkage, and good adhesion.
Mix the epoxy resin and hardener: Most underfill epoxy resins come in a two-part kit, with the resin and hardener packaged separately. Mix the two parts together according to the manufacturer’s instructions.
Add filler materials: Add filler materials to the epoxy resin mixture to increase its viscosity and provide additional structural support. Silica or glass beads are commonly used as fillers. Add the fillers slowly and mix thoroughly until the desired consistency is achieved.
Add solvents: Solvents can be added to the epoxy resin mixture to improve its flowability and wetting properties. Acetone or isopropyl alcohol are commonly used solvents. Add the solvents slowly and mix thoroughly until the desired consistency is achieved.
Optional: Add catalysts: Catalysts can be added to the epoxy resin mixture to accelerate the curing process. However, triggers can also reduce the pot life of the mix, so use them sparingly. Follow the manufacturer’s instructions for the appropriate amount of catalyst to add.
Apply the underfill epoxy resin to fill the epoxy resin mixture to the gap or joint. Use a syringe or dispenser to apply the mix precisely and avoid air bubbles. Ensure that the mixture is evenly distributed and covers all surfaces.
Cure the epoxy resin: The epoxy resin can cure according to the manufacturer’s instructions. Most underfill epoxy resins cure at room temperature, but some may require elevated temperatures for faster curing.
Are There Any Limitations Or Challenges Associated With Epoxy Underfill?
Yes, there are limitations and challenges associated with epoxy underfill. Some of the common limitations and challenges are:
Thermal expansion mismatch: Epoxy underfills have a coefficient of thermal expansion (CTE) that is different from the CTE of the components used to fill. This can cause thermal stresses and can lead to component failures, particularly in high-temperature environments.
Processing challenges: Epoxy underfills specialized processing equipment and techniques, including dispensing and curing equipment. If not done correctly, the underfill may not properly fill the gaps between components or may cause damage to the components.
Moisture sensitivity: Epoxy underfills are sensitive to moisture and can absorb moisture from the environment. This can cause issues with adhesion and can lead to component failures.
Chemical compatibility: Epoxy underfills can react with some materials used in electronic components, such as solder masks, adhesives, and fluxes. This can cause issues with adhesion and can lead to component failures.
Cost: Epoxy underfills can be more expensive than other underfill materials, such as capillary underfills. This can make them less attractive for use in high-volume production environments.
Environmental concerns: Epoxy underfill can contain hazardous chemicals and materials, such as bisphenol A (BPA) and phthalates, which can pose a risk to human health and the environment. Manufacturers must take proper precautions to ensure these materials’ safe handling and disposal.
Curing time: Epoxy underfill requires a certain amount of time to cure before it can be used in the application. The curing time can vary depending on the specific formulation of the underfill, but it typically ranges from several minutes to several hours. This can slow down the manufacturing process and increase the overall production time.
While epoxy underfills offer many benefits, including improved reliability and durability of electronic components, they also present some challenges and limitations that must be carefully considered before use.
What Are The Advantages Of Using Epoxy Underfill?
Here are some of the advantages of using epoxy underfill:
Step 1: Increased reliability
One of the most significant advantages of using epoxy underfill is increased reliability. Electronic components are vulnerable to damage due to thermal and mechanical stresses, such as thermal cycling, vibration, and shock. Epoxy underfill helps to protect the solder joints on electronic components from damage due to these stresses, which can increase the reliability and lifespan of the electronic device.
Step 2: Improved performance
By reducing the risk of damage to electronic components, epoxy underfill can help improve the device’s overall performance. Not correctly reinforced electronic components can suffer from reduced functionality or even complete failure, and epoxy underfills can help to prevent these issues, leading to a more reliable and high-performing device.
Step 3: Better thermal management
Epoxy underfill has excellent thermal conductivity, which helps dissipate heat from the electronic components. This can improve the thermal management of the device and prevent overheating. Overheating can cause damage to electronic components and lead to performance issues or even complete failure. By providing effective thermal management, epoxy underfill can prevent these problems and improve the overall performance and lifespan of the device.
Step 4: Enhanced mechanical strength
Epoxy underfill provides additional mechanical support to the electronic components, which can help to prevent damage due to vibration or shock. Not adequately reinforced electronic components can suffer from mechanical stress, leading to injury or complete failure. Epoxy can help to prevent these issues by providing additional mechanical strength, leading to a more reliable and durable device.
Step 5: Reduced warpage
Epoxy underfill can help reduce the PCB’s warpage during the soldering process, which can lead to improved reliability and better solder joint quality. PCB warpage can cause issues with the alignment of the electronic components, leading to common solder defects that can cause reliability issues or complete failure. Epoxy underfill can help prevent these issues by reducing warpage during manufacturing.
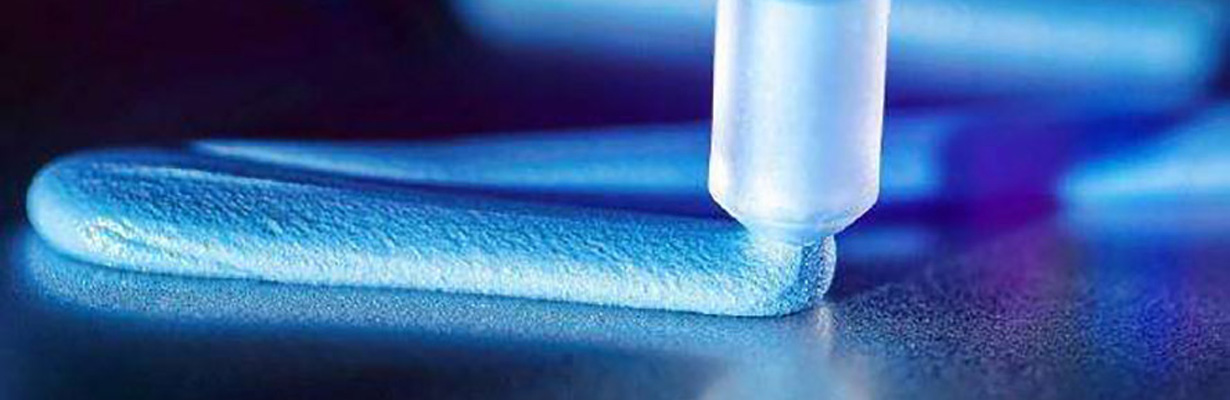
How Is Epoxy Underfill Applied In Electronics Manufacturing?
Here are the steps involved in applying epoxy underfill in electronics manufacturing:
Preparing the components: The electronic components must be designed before applying epoxy underfill. The components are cleaned to remove any dirt, dust, or debris that may interfere with the adhesion of the epoxy. The components are then placed on the PCB and held using a temporary adhesive.
Dispensing the epoxy: The epoxy underfill is dispensed onto the PCB using a dispensing machine. The dispensing machine is calibrated to dispense the epoxy in a precise amount and location. The epoxy is dispensed in a continuous stream along the edge of the component. The stream of epoxy should be long enough to cover the entire gap between the element and the PCB.
Spreading the epoxy: After dispensing it, it must be spread out to cover the gap between the component and the PCB. This can be done manually using a small brush or an automated spreading machine. The epoxy needs to be spread evenly without leaving any voids or air bubbles.
Curing the epoxy: The epoxy underfill is then fixed to harden and form a solid bond between the component and the PCB. The curing process can be done in two ways: thermal or UV. In thermal curing, the PCB is placed in an oven and heated to a specific temperature for a particular time. In UV curing, the epoxy is exposed to ultraviolet light to initiate the curing process.
Cleaning up: After the epoxy underfills are cured, excess epoxy can be removed using a scraper or a solvent. It is essential to remove any excess epoxy to prevent it from interfering with the performance of the electronic component.
What Are Some Typical Applications Of Epoxy Underfill?
Here are some typical applications of epoxy underfill:
Semiconductor packaging: Epoxy underfill is widely used in the packaging of semiconductor devices, such as microprocessors, integrated circuits (ICs), and flip-chip packages. In this application, epoxy underfill fills the gap between the semiconductor chip and the substrate, providing mechanical reinforcement and enhancing thermal conductivity to dissipate heat generated during operation.
Printed circuit board (PCB) assembly: Epoxy underfill is used in the body of PCBs to enhance the reliability of solder joints. It is applied to the underside of components such as ball grid array (BGA) and chip scale package (CSP) devices before reflow soldering. The epoxy underfills flow into the gaps between the component and the PCB, forming a strong bond that helps to prevent solder joint failures due to mechanical stresses, such as thermal cycling and shock/vibration.
Optoelectronics: Epoxy underfill is also used in packaging optoelectronic devices, such as light-emitting diodes (LEDs) and laser diodes. These devices generate heat during operation, and epoxy underfills help to dissipate this heat and improve the overall thermal performance of the device. Additionally, epoxy underfill provides mechanical reinforcement to protect delicate optoelectronic components from mechanical stresses and environmental factors.
Automotive electronics: Epoxy underfill is utilized in automotive electronics for various applications, such as engine control units (ECUs), transmission control units (TCUs), and sensors. These electronic components are subjected to harsh environmental conditions, including high temperatures, humidity, and vibration. Epoxy underfill protects against these conditions, ensuring reliable performance and long-term durability.
Consumer electronics: Epoxy underfill is used in various consumer electronic devices, including smartphones, tablets, gaming consoles, and wearable devices. It helps to improve these devices’ mechanical integrity and thermal performance, ensuring reliable operation under various usage conditions.
Aerospace and defense: Epoxy underfill is employed in aerospace and defense applications, where electronic components must withstand extreme environments, such as high temperatures, high altitudes, and severe vibrations. Epoxy underfill provides mechanical stability and thermal management, making it suitable for rugged and demanding environments.
What Are The Curing Processes For Epoxy Underfill?
The curing process for epoxy underfill involves the following steps:
Dispensing: Epoxy underfill is typically dispensed as a liquid material onto the substrate or chip using a dispenser or a jetting system. The epoxy is applied in a precise manner to cover the entire area that needs to be underfilled.
Encapsulation: Once the epoxy is dispensed, the chip is usually placed on top of the substrate, and the epoxy underfill flows around and underneath the chip, encapsulating it. The epoxy material is designed to flow easily and fill gaps between the chip and substrate to form a uniform layer.
Pre-curing: The epoxy underfill is typically pre-cured or partially cured to a gel-like consistency after encapsulation. This is done by subjecting the assembly to a low-temperature curing process, such as oven baking or infrared (IR). The pre-curing step helps reduce the epoxy’s viscosity and prevents it from flowing out of the underfill area during the subsequent curing steps.
Post-curing: Once the epoxy underfills are pre-cured, the assembly is subjected to a higher-temperature curing process, typically in a convection oven or a curing chamber. This step is known as post-curing or final curing, and it is done to fully cure the epoxy material and achieve its maximum mechanical and thermal properties. The time and temperature of the post-curing process are carefully controlled to ensure complete curing of the epoxy underfill.
Cooling: After the post-curing process, the assembly is usually allowed to cool down to room temperature slowly. Rapid cooling can cause thermal stresses and affect the integrity of the epoxy underfill, so controlled cooling is essential to avoid any potential issues.
Inspection: Once the epoxy underfills are fully cured, and the assembly has cooled down, it is typically inspected for any defects or voids in the underfill material. X-ray or other non-destructive testing methods may be used to check the quality of the epoxy underfill and ensure that it has adequately bonded the chip and substrate.
What Are The Different Types Of Epoxy Underfill Materials Available?
Several types of epoxy underfill materials are available, each with its own properties and characteristics. Some of the common types of epoxy underfill materials are:
Capillary Underfill: Capillary underfill materials are low-viscosity epoxy resins that flow into the narrow gaps between a semiconductor chip and its substrate during the underfill process. They are designed to have low viscosity, allowing them to easily flow into small gaps through capillary action, and then cure to form a rigid, thermosetting material that provides mechanical reinforcement to the chip-substrate assembly.
No-Flow Underfill: As the name suggests, no-flow underfill materials do not flow during the underfill process. They are typically formulated with high-viscosity epoxy resins and are applied as a pre-dispensed epoxy paste or film on the substrate. During the assembly process, the chip is placed on top of the no-flow underfill, and the assembly is subjected to heat and pressure, causing the epoxy to cure and form a rigid material that fills the gaps between the chip and the substrate.
Molded Underfill: Molded underfill materials are pre-molded epoxy resins placed on the substrate and then heated to flow and encapsulate the chip during the underfill process. They are typically used in applications where high-volume manufacturing and precise control of underfill material placement are required.
Wafer-Level Underfill: Wafer-level underfill materials are epoxy resins applied to the entire wafer surface before the individual chips are singulated. The epoxy is then cured, forming a rigid material that provides underfill protection to all the chips on the wafer. Wafer-level underfill is typically used in wafer-level packaging (WLP) processes, where multiple chips are packaged together on a single wafer before being separated into individual packages.
Encapsulant Underfill: Encapsulant underfill materials are epoxy resins used to encapsulate the entire chip and substrate assembly, forming a protective barrier around the components. They are typically used in applications requiring high mechanical strength, environmental protection, and enhanced reliability.
Related Sources About Epoxy Adhesive Glue:
Epoxy underfill chip level adhesives
One Component Epoxy Underfill Encapsulant
Low Temperature Cure BGA Flip Chip Underfill PCB Epoxy
Epoxy-Based Chip Underfill And COB Encapsulation Materials
Flip-Chip And BGA Underfills Process Epoxy Adhesive Glue
The Benefits And Applications Of Underfill Epoxy Encapsulants In Electronics
How to use a smt underfill epoxy adhesive in various applications
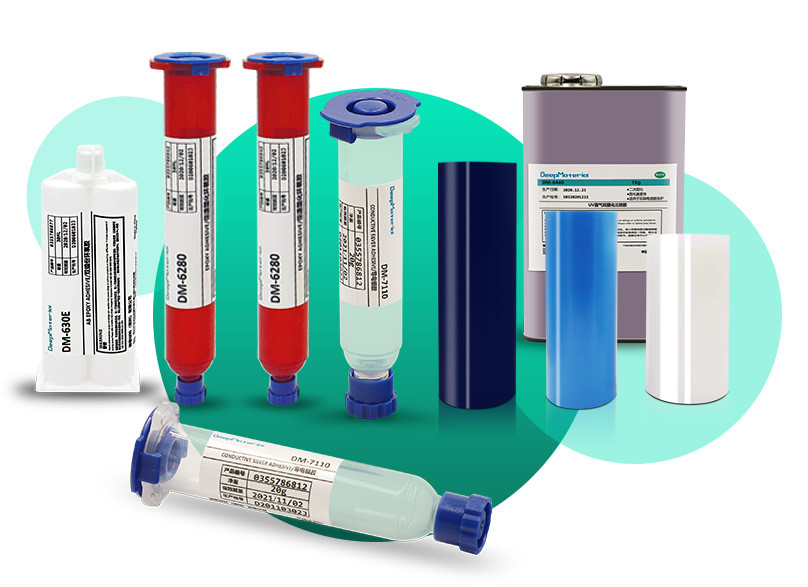
About BGA Underfill Epoxy Adhesive Manufacturer
Deepmaterial is reactive hot melt pressure sensitive adhesive manufacturer and supplier, manufacturing underfill epoxy,one component epoxy adhesive, two component epoxy adhesive,hot melt adhesives glue, uv curing adhesives,high refractive index optical adhesive, magnet bonding adhesives, best top waterproof structural adhesive glue for plastic to metal and glass, electronic adhesives glue for electric motor and micro motors in home appliance.
HIGH QUALITY ASSURANCE
Deepmaterial is determined to become a leader in the electronic underfill epoxy industry, quality is our culture!
FACTORY WHOLESALE PRICE
We promise to let customers get the most cost-effective epoxy adhesives products
PROFESSIONAL MANUFACTURERS
With electronic underfill epoxy adhesive as the core, integrating channels and technologies
RELIABLE SERVICE ASSURANCE
Provide epoxy adhesives OEM, ODM, 1 MOQ.Full Set of Certificate
Safe Fireproof Glue for Home Use
Safe Fireproof Glue for Home Use In today’s homes, safety is a top priority, especially when it comes to the materials we use for construction, repairs, or DIY projects. One often overlooked but critical component is the adhesive or glue employed in these tasks. While most glues are designed for...
Flame Retardant Adhesive for Circuit Boards
Flame Retardant Adhesive for Circuit Boards In the fast-paced world of modern electronics, where circuit boards power everything from smartphones to vehicle control systems, safety and reliability are paramount. Flame retardant adhesives for circuit boards are specialized bonding agents designed to secure components, provide insulation, and prevent fire hazards in...
Exploration of the Limitations and Complementarity of Fire Retardant Materials Testing Methods
Exploration of the Limitations and Complementarity of Fire Retardant Materials Testing Methods In the fields of materials science and fire safety, fire retardant materials play a crucial role. To evaluate their performance, international and national standards such as ISO, ASTM, and GB have been established. Commonly used testing methods include...
Synergistic Enhancement Mechanism of Gas-Phase, Condensed-Phase, and Heat-Exchange Interruption Flame Retardant Mechanisms
Synergistic Enhancement Mechanism of Gas-Phase, Condensed-Phase, and Heat-Exchange Interruption Flame Retardant Mechanisms With the widespread application of polymer materials in fields such as construction, electronics, and transportation, the flame retardant properties of materials have become increasingly important. A single flame retardant mechanism often struggles to meet complex flame retardant requirements,...
How to More Accurately Evaluate the Comprehensive Fireproof Effect of Fireproof Adhesives by Simulating Actual Fire Scenarios
How to More Accurately Evaluate the Comprehensive Fireproof Effect of Fireproof Adhesives by Simulating Actual Fire Scenarios Fireproof adhesives play a critical role in fire safety across numerous fields, including construction, electronics, and transportation. Accurately evaluating the comprehensive fireproof effect of fireproof adhesives is of paramount importance for ensuring human...
Research on Influencing Factors and Protective Measures of Fireproof Adhesive Performance in High-Temperature, High-Humidity, and Chemical Corrosion Environments
Research on Influencing Factors and Protective Measures of Fireproof Adhesive Performance in High-Temperature, High-Humidity, and Chemical Corrosion Environments Fireproof adhesive, as a critical fire-resistant material, is widely used in numerous fields such as construction, electronics, and automotive industries, playing a vital role in preventing fire spread and safeguarding life and...