Customizing the Properties of UV Cure Silicone Adhesive for Specific Applications
Customizing the Properties of UV Cure Silicone Adhesive for Specific Applications
UV cure silicone adhesive is a handy glue used in lots of industries because it dries fast, sticks really well, and can handle heat, chemicals, and weather great. But, not every job needs the same glue features, so it’s important to make the glue fit the specific job. This way, companies can get the best performance, cut down on costs and waste, and stick to rules and standards.
To make UV cure silicone adhesive just right for a job, you need to know what it’s made of and how it dries. This glue is mainly made from a type of polymer that includes silicon. It dries solid when hit with UV light due to a chemical reaction.
There are also other features of the glue you can change, like viscosity (how thick or runny it is), hardness (how tough it is against pressure), and elasticity (how stretchy it is). Plus, how well it can stand up to heat and chemicals can also be adjusted for different uses.
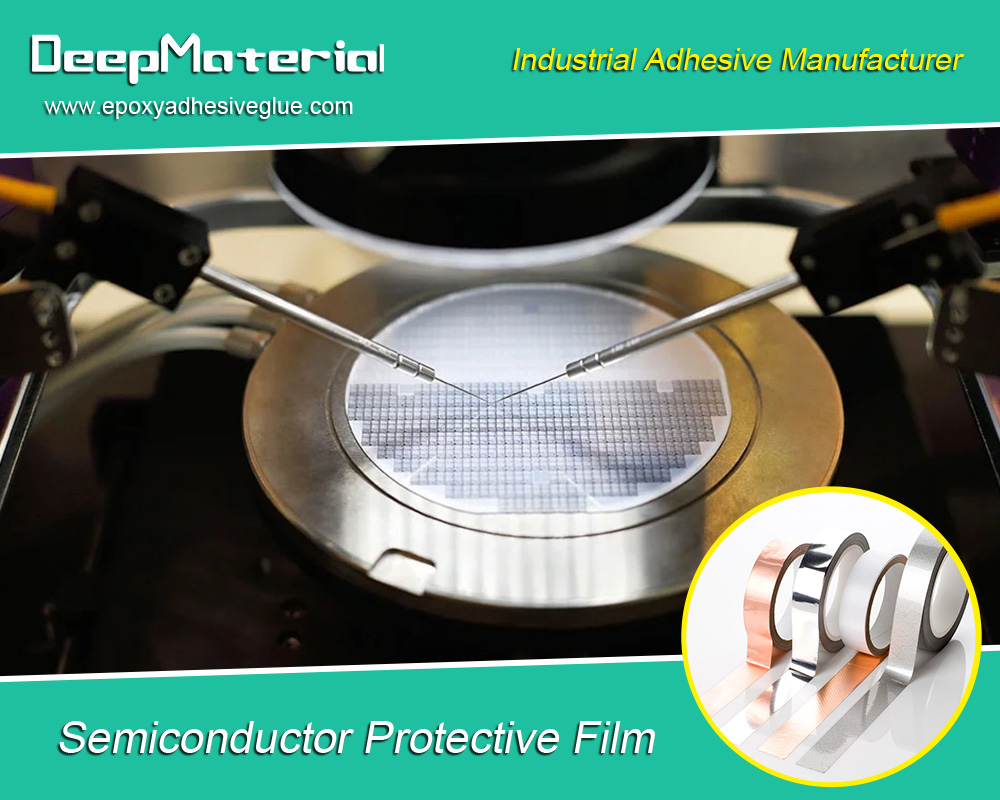
Importance of Customizing UV Cure Silicone Adhesive
Making the glue fit for a particular job is key for it to work best. Every industry has its own needs. For instance, in the medical field, it’s important for the glue to be safe for the body and able to be cleaned well. In electronics, it’s about managing heat and not messing with electricity. By changing the glue’s properties, companies can make sure it does exactly what they need.
Adjusting the glue also helps save money and reduce waste. If the glue is just right for the job, you don’t need to use more than necessary, which can save money and is better for the planet.
Lastly, making the glue meet specific industry rules and certifications is a must. Different jobs might have strict requirements for what the glue needs to do. By tweaking the glue to meet these needs, companies can be sure their products are good to go for their intended use.
Factors to Consider When Customizing UV Cure Silicone Adhesive
When tweaking UV cure silicone adhesive for specific uses, you need to think about a few key things. First, the type of material you’re sticking to matters a lot because different materials bond better with different kinds of glue.
Also, the environment where the adhesive will be used is important. Things like temperature, wetness, and exposure to chemicals or sunlight can change how well the adhesive works. Making sure the glue can handle these conditions is key for it to last.
How you put the glue on makes a difference too. Whether you’re spraying, pouring, or dipping could change the kind of glue formula you need.
And, you should be really clear about what you want the glue to do. Things like how strong the bond needs to be, how much it can bend, how it handles heat, and how it deals with chemicals need to be considered. Knowing all this helps make the glue just right.
Techniques for Customizing UV Cure Silicone Adhesive
To customize UV cure silicone adhesive, you can mix in special ingredients or fillers to improve things like flexibility, stickiness, or even electrical properties. Using different crosslinking agents can make the glue tougher and last longer.
You can also play around with how much UV light the glue gets and for how long. More light or longer times can make the bond stronger or make the glue dry faster.
Even the way you mix and cure the glue can be adjusted. The temperature, how moist the air is, and how fast you mix can all change the glue’s characteristics. By controlling these factors, you can get the glue to perform exactly how you need it to.
Customizing UV Cure Silicone Adhesive for Specific Applications
Customizing this type of adhesive is super important for lots of fields. In medical uses, the glue needs to be safe for the body and able to stay strong even when sterilized. It also needs to stick to skin and body tissues without issues.
For electronics, being able to conduct heat well and insulate electrical parts is key. It also has to stick well to metals, plastics, and glass.
In cars, the adhesive has to be able to deal with heat, oil, and shaking (vibration)—stuff that’s common under the hood or around the engine.
And for space missions, the glue needs to not give off gases that could mess with equipment, handle super high temperatures, and stick to composite materials.
Each of these applications has its own special requirements, showing just how versatile and customizable UV cure silicone adhesive can be.
Testing and Quality Control of Customized UV Cure Silicone Adhesive
Making sure customized UV cure silicone adhesive is top-notch requires careful testing and quality control. Tests for things like how much it can stretch, how hard it is, and how well it can bend are important. It’s also key to check how the adhesive holds up against different chemicals.
Testing how well the adhesive sticks to various materials is super important. This can involve methods like peel testing or lap shear testing to measure the strength of the bond.
Quality control during the making of the adhesive helps make sure it’s always reliable and consistent. This means keeping an eye on the materials used, how it’s made, and testing the final product.
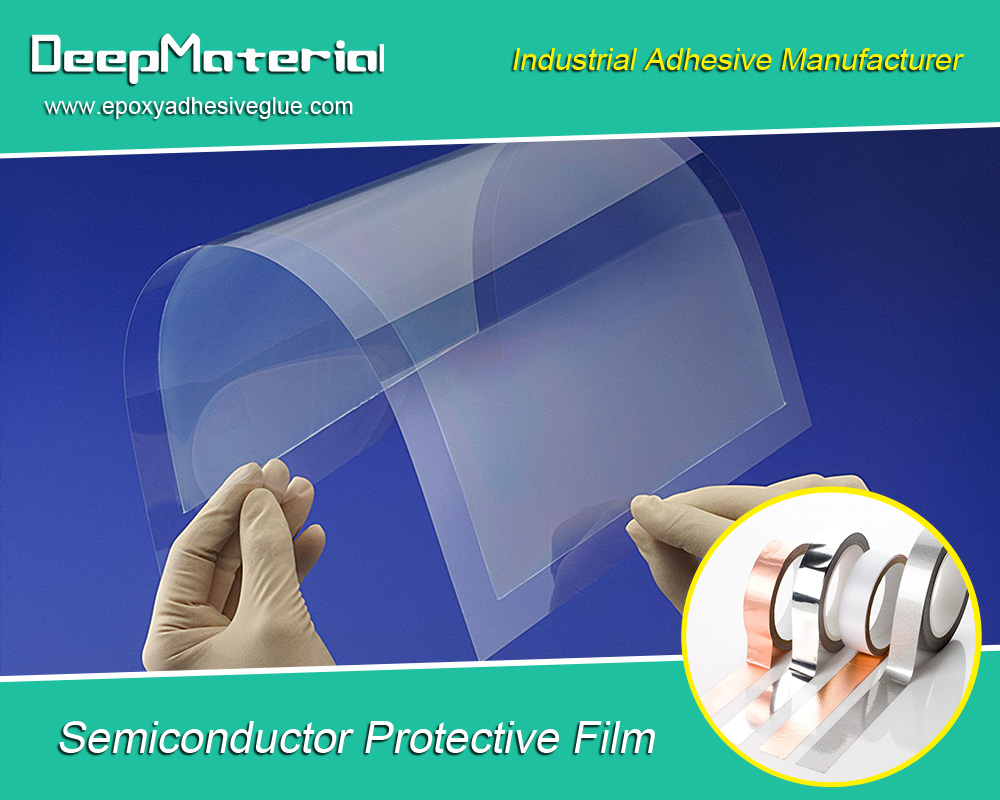
Conclusion and Future Developments in Customizing UV Cure Silicone Adhesive
In short, tailoring UV cure silicone adhesive is key for the best performance, saving money, and sticking to rules and standards. Knowing about the adhesive’s features and thinking about things like what it’s sticking to, the surroundings, how it’s applied, and what it needs to do helps make the adhesive perfect for the job.
Using special ingredients, tweaking how much UV light it gets, and making sure the mixing and curing are just right are ways to customize the adhesive. Since different jobs have different needs, being able to change the adhesive is super useful.
Looking ahead, there’s a lot of room for new ideas and improvements in UV cure silicone adhesive. With new materials and tech coming out, there’s a chance to make even better adhesives. Working together, the people who make the adhesives and the ones who use them can help drive these innovations, making sure the adhesive keeps up with the changing needs of different industries.
For more about choosing the Properties of UV Cure Silicone Adhesive for Specific Applications, you can pay a visit to DeepMaterial at https://www.epoxyadhesiveglue.com/category/epoxy-adhesives-glue/ for more info.