Does UV-Curing Plastic Bonding Adhesives Require Extreme Temperatures?
Does UV-Curing Plastic Bonding Adhesives Require Extreme Temperatures?
When welding plastic materials, adhesives are necessary for attaining powerful and resilient bonds. But with all the adhesive options, UV-curing plastic-bonding adhesives are rising in popularity because of their fast cure time and exceptional strength properties.
Unfortunately, though, many people falsely assume that these types of glues need scorching temps to function properly. In this article, we’ll dive into that misconception by looking closer at the temperature needs of UV-curing plastic bonding adhesives – let’s shine some light on the truth!
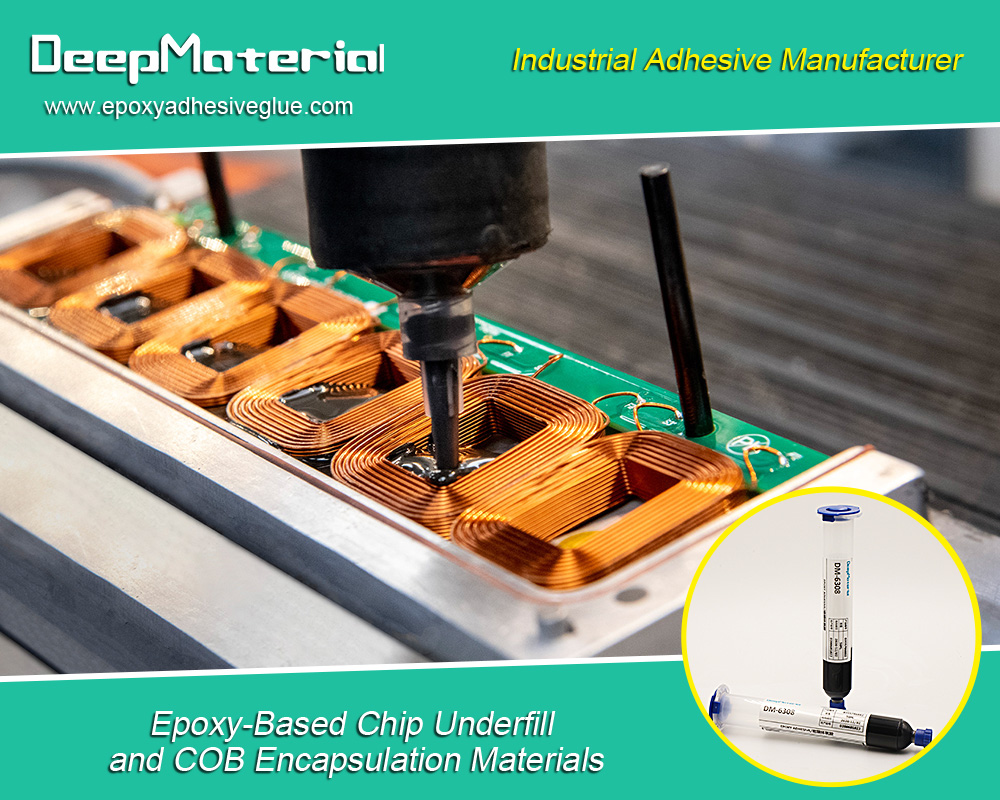
The Role of Temperature in Bonding
Meddling with temperatures has always been an important aspect of welding parts and definitely can’t be ignored when using adhesives. The temperature at which you apply the sealant and cure it affects how strong and long-lasting your bond will be – so remember that higher temps generally quicken up those reactions between the adhesive and surface!
We all know hotter temperatures make adhesives dry quicker and create sturdy bonds – but this isn’t always true. Different glues have additional heat requirements to perform their best; some may even need scorching temperatures, while others may be more sensitive to warmth and demand cooler conditions so they don’t break down. So, it’s essential to remember not all binders are made equal!
It’s critical to follow the manufacturer’s directions when handling adhesives – humidity and pressure greatly impact curing, which can make or break your bonds. To guarantee strong, durable results, watch for environmental changes like temperature shifts; pay attention, and you won’t be disappointed!
Temperature Range for UV Curing Adhesives
Surprising to many, UV-curing plastic bonding adhesives don’t need the high temperatures you might assume for it to seal tight. They’re made to work their magic at normal room temperature or slightly above – between 20°C and 40°C (68°F and 104°F). Amazingly, an adhesive can take hold in a common range without extreme heat!
UV-curing adhesives are a snap to use: there’s no need for special equipment or processes, and they don’t require any high heat, making them an incredibly versatile choice when bonding plastics. Moreover, since you can do without extreme temperatures, these adhesives make it easy on your wallet and Mother Nature!
Sure, UV-curing plastic bonding adhesives are a win for all your plastic bonding needs. And their ability to harden even if there’s just the tiniest bit of heat in the room is incredible; no wonder so many people are into them! What’s not to love about an adhesive that can get all your projects done with such remarkable ease?
Benefits of Low-Temperature Curing
UV-curing adhesives are a godsend with their low-temperature cure capabilities, skirting the need to invest in high-heat systems. Manufacturers who want eco-friendly production processes and save on energy costs reap great benefits here – talk about killing two birds with one stone! Plus, by avoiding expensive ovens at scorching temperatures, these clever adhesives can lighten up your carbon footprint and pocketbook.
Low-temp curing is a blessing for delicate substrates, protecting them against thermal harm. Plus, UV adhesives are perfect for production cycles – their short cure times at low temperatures mean more output with the same attention to quality and efficiency. All that without risk of damage or deformation; talk about convenience!
Factors Affecting Curing Time
UV-curing adhesives are a top option for bonding applications, as they can get the job done quickly and efficiently. Although these glues typically take little time to set, their curing rate depends on certain variables – like the amount of adhesive used. If you lay it on a bit thicker than usual, you may need to allow extra time; ultraviolet light needs greater depth to cure dense layers effectively!
It’s important to consider the curing time when selecting a UV light source for an adhesive. Higher-intensity sources that pack a punch will cut down on your wait time – and if you’re using the wrong formulation, you’ll be waiting longer than necessary. So, pick those high-intensity rays and the right composition to guarantee efficient curing!
Importance of Proper UV Light Exposure
The temperature may sound insignificant regarding UV-curing adhesives, but having the right amount of sunshine does matter – otherwise, you could be up a creek without a paddle! Too little exposure, and your bonds can go from strong to weak in seconds. More light means incomplete polymerization and possibly poor product performance. Bottom line: ensuring all your adhesive gets exposed to just the right dose of rays for optimal bond formation is essential.
Controlling Temperature During Curing
Taking care of the temperature during curing is paramount when dealing with UV-curing adhesives – it’s so impactful that failure to control it would impair the adhesive’s potency in terms of strength and stability. Monitoring and regulation should stay top-of-mind to prevent this, as they’ll guarantee optimal performance for even the most demanding applications. Ultimately, keep yourself from getting too hotheaded or neglecting temperature management – doing either could lead to seriously sticky results.
Application Considerations
It’s a must to carefully pick the best UV-curing plastic bonding adhesive, which is critical for the longevity and quality of the bonded items. Make sure you are extra vigilant when evaluating what will suit your needs. Specifically, any application involving high temperatures should be conducted with an adhesive that can handle it without sacrificing its bond strength; otherwise, you’re looking at disrepair down the line!
On top of that, if flexibility is also key in your scenario, ensure your adhesive provides just that – otherwise, nothing short of rupture can be expected when put under duress! Ultimately, by taking detailed consideration into all variable requirements, you’ll end up with an adhesive furnished to maintain optimal performance while preserving its bonding properties over time.
Final words
To summarize, UV-cure plastic bonders don’t need sweltering heat for their stickiness to work. These bonders are made to cure at room temperature or a bit above – usually between 68 and 104 Fahrenheit. This offers advantages like less spent money, safer worksites, and faster manufacturing cycles. Controlling the temperature during hardening is important, but exposure to ultraviolet light will ultimately give you salute-worthy bonding results!
For more about choosing the UV-Curing Plastic Bonding Adhesives, you can pay a visit to DeepMaterial at https://www.epoxyadhesiveglue.com/category/epoxy-adhesives-glue/ for more info.