The Key Role of Molecular Structure Design in Balancing the Performance of Fireproof Adhesives
The Key Role of Molecular Structure Design in Balancing the Performance of Fireproof Adhesives
Fireproof adhesives serve as critical functional materials in modern industry and construction, with their performance directly impacting the safety and reliability of relevant application scenarios. As technology advances, the requirements for fireproof adhesives have become increasingly stringent. They are expected to possess excellent flame retardancy to effectively suppress fire spread and reduce fire risks, high bonding strength to ensure firm adhesion of bonded objects and maintain structural stability, as well as good aging resistance to guarantee long-term performance stability and reduce maintenance and replacement costs. Molecular structure design, such as introducing flame-retardant groups containing phosphorus, nitrogen, halogens, etc., provides a key pathway to achieve a balance among these properties.

Basic Composition and Performance Requirements of Fireproof Adhesives
Basic Composition
Fireproof adhesives generally consist of binders, curing agents, flame retardants, and other additives. The binder, as the main component, determines the basic properties of the fireproof adhesive, with common types including epoxy resins, phenolic resins, and silicone resins. Curing agents trigger cross-linking reactions in the binder to form a three-dimensional network structure, thereby enhancing the hardness, strength, and heat resistance of the adhesive. Flame retardants are key additives that endow fireproof adhesives with flame-retardant properties, while other additives such as plasticizers and coupling agents can improve the processing performance, flexibility, and bonding properties of the adhesive.
Performance Requirements
- Flame Retardancy: In the event of a fire, fireproof adhesives must rapidly act to prevent flame propagation and reduce heat release, buying precious time for personnel evacuation and fire fighting. The quality of their flame-retardant performance directly affects the severity of fire hazards.
- Bonding Strength: The adhesive must securely bond the adherends under various environmental conditions, ensuring no debonding occurs during normal use or extreme situations like fires, thus maintaining structural integrity.
- Aging Resistance: Over long-term use, fireproof adhesives are subject to environmental factors such as temperature, humidity, light, and oxygen, which can gradually degrade their performance. Good aging resistance ensures that fireproof adhesives maintain their required properties throughout their specified service life, reducing performance failures and safety hazards caused by aging.
Mechanisms of Molecular Structure Design on Fireproof Adhesive Performance
Roles of Flame-Retardant Groups
- Phosphorus-Containing Groups: When heated, phosphorus-containing flame retardants decompose to generate substances such as phosphoric acid and metaphosphoric acid. These products have strong dehydrating effects, promoting surface carbonization of the material to form a dense char layer. This char layer isolates oxygen and heat, preventing further fire spread and achieving flame retardancy. Additionally, phosphorus compounds can capture free radicals in the gas phase to inhibit combustion reactions.
- Nitrogen-Containing Groups: Upon thermal decomposition, nitrogen-containing flame retardants release non-combustible gases such as nitrogen and ammonia, which dilute the oxygen concentration in the air and suppress combustion by reducing the oxygen content in the burning zone. Meanwhile, free radicals generated from nitrogen-containing compounds can react with active free radicals during combustion to terminate the radical chain reaction, contributing to flame retardancy. Some nitrogen-containing flame retardants also form expandable char layers with thermal insulation properties after decomposition, further enhancing flame retardancy.
- Halogen-Containing Groups: During combustion, halogen atoms in halogen-containing flame retardants combine with hydrogen and oxygen radicals in the flame to generate hydrogen halide gases. These gases capture free radicals in the flame, interrupting the combustion chain reaction and achieving flame retardancy. However, halogen-containing flame retardants may produce toxic and harmful gases during combustion, posing risks to the environment and human health. Consequently, their use is restricted in some environmentally sensitive fields, gradually being replaced by halogen-free flame retardants.
Impact on Bonding Strength
Changes in molecular structure affect the interaction between the fireproof adhesive and the adherend. Flame-retardant groups with appropriate polarity and reactivity can form chemical bonds, hydrogen bonds, or van der Waals forces with groups on the adherend surface, thereby enhancing bonding strength. For example, some flame retardants with polar groups such as hydroxyl (-OH) or amino (-NH₂) can chemically react with active sites on the surface of polar materials like metals and glass to form strong chemical bonds, improving bonding performance. However, introducing flame-retardant groups that disrupt the regularity and flexibility of the binder molecules may weaken intermolecular forces, reducing bonding strength. Therefore, molecular structure design must comprehensively consider the type, quantity, and position of flame-retardant groups to balance flame retardancy and bonding strength.
Impact on Aging Resistance
Reasonable molecular structure design can improve the aging resistance of fireproof adhesives. Introducing chemical bonds or groups with high stability enhances the molecular chain’s resistance to degradation by external environmental factors. For instance, silicone resins containing silicon-oxygen (Si-O) bonds have high bond energy, endowing them with excellent heat resistance, weather resistance, and chemical stability. Incorporating silicone structures into fireproof adhesives can significantly improve their aging resistance. Additionally, groups or additives with anti-oxidation and UV resistance properties, such as hindered phenol antioxidants and UV absorbers, can be introduced into the adhesive’s molecular structure through chemical bonding or physical blending to effectively inhibit molecular chain degradation caused by oxidation and UV radiation, prolonging the adhesive’s service life.
Molecular Structure Design Strategies for Balancing Adhesive Performance
Selection of Suitable Flame-Retardant Groups
- Choose appropriate flame-retardant groups based on the application scenario and environmental/performance requirements. In environmentally sensitive fields such as interior decoration and electronics, prioritize halogen-free flame-retardant groups (e.g., phosphorus- and nitrogen-containing compounds). For industrial applications with extremely high flame-retardant requirements and relatively lower toxicity concerns, halogen-containing flame-retardant groups may be used appropriately, but their dosage and emissions must be controlled.
- Optimize the structure and proportion of flame-retardant groups. Different flame-retardant group structures exhibit varying flame-retardant effects and impacts on other properties. Through experiments and theoretical calculations, study the synergistic effects of different structures to identify the optimal combination and proportion, maximizing flame retardancy while minimizing negative impacts on bonding strength and aging resistance. For example, combining phosphorus- and nitrogen-containing flame-retardant groups leverages their synergistic flame retardancy in both the gas and condensed phases, improving efficiency and reducing total additive usage, thereby mitigating adverse effects on other properties.
Regulation of Molecular Chain Structure
- Adjust molecular chain length and molecular weight distribution. Moderately increasing molecular chain length can enhance intermolecular entanglement, improving the adhesive’s cohesive strength and bonding strength. However, excessively long chains may reduce molecular mobility, affecting processing performance and curing speed. Additionally, control the uniformity of molecular weight distribution to avoid excessively large or small chains, as the former increases system viscosity and hinders processing, while the latter reduces cohesive and bonding strengths.
- Introduce flexible or rigid segments. Incorporating flexible segments (e.g., polyether or polyester chains) into molecular chains can improve the adhesive’s flexibility and impact resistance, enhancing its bonding performance under complex stress conditions. Excessive flexible segments, however, may reduce heat resistance and flame retardancy. Conversely, introducing rigid segments (e.g., benzene or naphthalene rings) can increase molecular chain rigidity and heat resistance, enhancing flame retardancy and dimensional stability but potentially compromising flexibility and bonding performance. Therefore, the proportion and distribution of flexible and rigid segments must be rationally adjusted according to specific performance requirements.
Construction of Interpenetrating Network (IPN) Structures
Constructing interpenetrating network (IPN) structures allows the mutual penetration and entanglement of polymer networks with different properties, achieving complementary and synergistic performance. For example, combining a polymer network with excellent flame retardancy and another with high bonding strength into an IPN structure. In this structure, the two polymer networks mutually restrict and support each other, enhancing the adhesive’s overall mechanical and bonding properties while promoting uniform dispersion of flame retardants to strengthen flame retardancy. IPN structures also improve aging resistance, as interactions between different polymer networks inhibit molecular chain movement and degradation, enhancing system stability. Common IPN construction methods include sequential polymerization, simultaneous polymerization, and emulsion polymerization, each with its advantages, disadvantages, and applicable scenarios.
Surface Modification and Interface Optimization
- Surface modification of flame retardants. The dispersibility and compatibility of flame retardants in the adhesive matrix significantly affect overall performance. Surface modification techniques, such as treating flame retardants with coupling agents or surfactants, can improve their surface properties and enhance dispersibility and compatibility in the matrix. For example, silane coupling agents can react with active groups on the surface of phosphorus-containing flame retardants at one end and chemically bond or physically entangle with the binder at the other end, strengthening the interface between flame retardants and the matrix and improving comprehensive performance.
- Optimization of the adhesive-adherend interface. Molecular structure design can introduce functional groups or additives to improve interface performance. For instance, adding surfactants or tackifiers with good wettability can reduce interfacial tension, enhance the adhesive’s wetting and spreading ability on the adherend surface, and improve bonding strength. Additionally, forming chemical bonds or adsorption layers at the interface through chemical reactions can significantly enhance interfacial bonding strength and stability, thereby improving aging resistance.
Experimental Verification and Data Analysis
Experimental Design
- Prepare a series of fireproof adhesive samples with different molecular structure designs by varying factors such as flame-retardant group types, contents, molecular chain structures, and IPN construction.
- Conduct flame-retardancy tests on each sample using methods such as vertical burning, horizontal burning, and limiting oxygen index (LOI) tests to evaluate flame-retardant performance and record data such as combustion time, flame spread rate, and oxygen index.
- Perform bonding strength tests using appropriate methods (e.g., tensile shear strength, peel strength) based on the adherend material to measure the adhesive’s bonding strength.
- Carry out aging resistance tests by simulating environmental factors (temperature, humidity, light) through accelerated aging experiments (thermal aging, damp-heat aging, UV aging). Regularly test sample performance during aging to record changes.
Data Analysis
- Analyze flame-retardancy test data to investigate the relationship between molecular structure design factors and flame-retardant performance. Through data fitting and statistical analysis, identify key factors and optimal parameter combinations influencing flame retardancy, and determine the impact of flame-retardant group types and contents on performance.
- Analyze bonding strength data to explore the influence mechanisms of molecular structure design. Compare bonding strength data across samples to study the correlation between factors like molecular chain structure and interface optimization and bonding strength, identifying effective design strategies to enhance bonding strength.
- Evaluate the performance stability of different molecular structure designs during aging through aging test data. By comparing pre- and post-aging performance, analyze the impact of molecular structure factors on aging resistance and identify design methods to improve durability. For example, thermal aging data may show that adhesives with silicon-oxygen bond structures exhibit significantly smaller declines in tensile strength and flame retardancy compared to those without, indicating the effectiveness of silicon-oxygen bonds in enhancing thermal aging resistance.
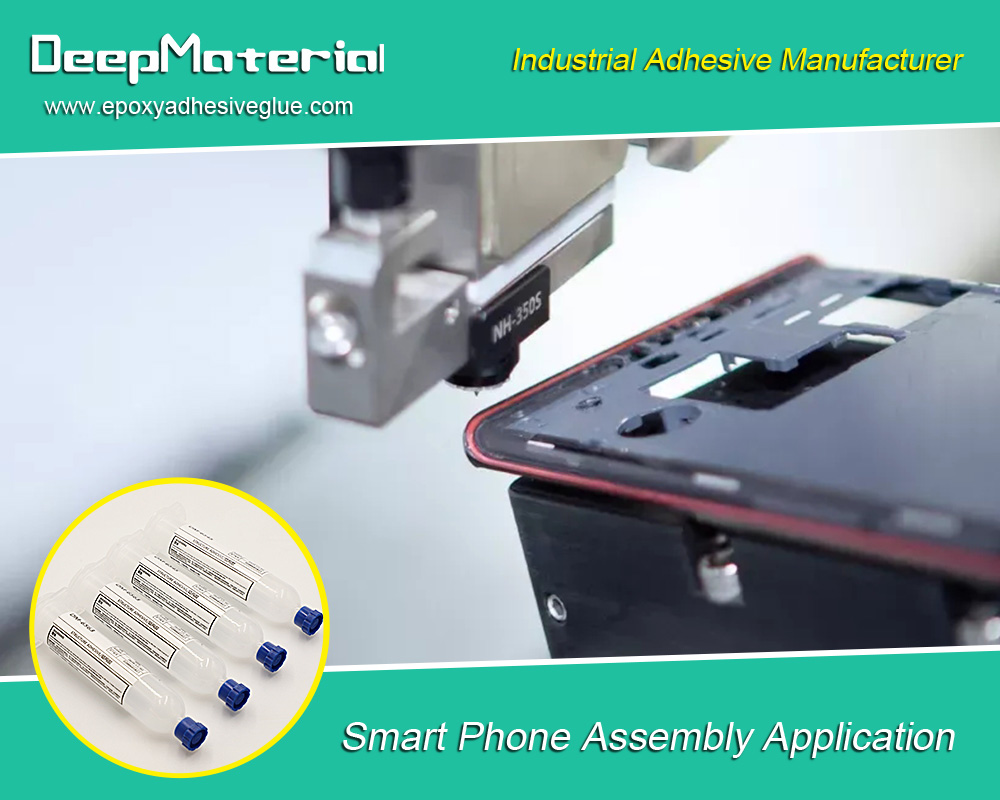
Conclusion and Outlook
Through molecular structure design—such as introducing flame-retardant groups containing phosphorus, nitrogen, halogens, etc.—and integrating strategies like regulating molecular chain structures, constructing IPN structures, and optimizing surfaces/interfaces, it is possible to effectively balance the flame retardancy, bonding strength, and aging resistance of fireproof adhesives. Experimental results demonstrate that rational molecular structure design can significantly improve the comprehensive performance of fireproof adhesives to meet diverse application needs. However, current research still has limitations, such as insufficient exploration of novel flame-retardant groups and molecular structures, incomplete understanding of structure-property relationships, and unresolved technical challenges in practical applications.
Future research should focus on developing more environmentally friendly and efficient flame-retardant groups and molecular structures, deepening the understanding of structure-property relationships, and enhancing the application of theoretical calculations and simulation technologies in molecular design to further improve adhesive performance and expand application fields. With the continuous development of materials science and technology, it is believed that more innovative molecular design methods will be applied to fireproof adhesive research, contributing to the protection of life and property and the advancement of related industries.
For more about choosing the key role of molecular structure design in balancing the performance of fireproof adhesives, you can pay a visit to DeepMaterial at https://www.epoxyadhesiveglue.com/category/epoxy-adhesives-glue/ for more info.