Flame Retardant Adhesive for Circuit Boards
Flame Retardant Adhesive for Circuit Boards
In the fast-paced world of modern electronics, where circuit boards power everything from smartphones to vehicle control systems, safety and reliability are paramount. Flame retardant adhesives for circuit boards are specialized bonding agents designed to secure components, provide insulation, and prevent fire hazards in environments prone to heat, electrical faults, or external ignition sources. These adhesives are critical in industries like automotive, aerospace, consumer electronics, and industrial manufacturing, where circuit board failures could lead to catastrophic fires or system malfunctions.
In the automotive industry, flame retardant adhesives are essential for bonding circuit boards in electronic control units (ECUs), infotainment systems, and electric vehicle (EV) power electronics, ensuring compliance with stringent fire safety standards while enhancing durability and performance. This article provides an in-depth exploration of flame retardant adhesives for circuit boards, covering their definition, types, properties, applications (with a strong focus on automotive), challenges, and emerging trends. By understanding their role, we gain insight into how these adhesives safeguard critical electronic systems in high-risk environments.
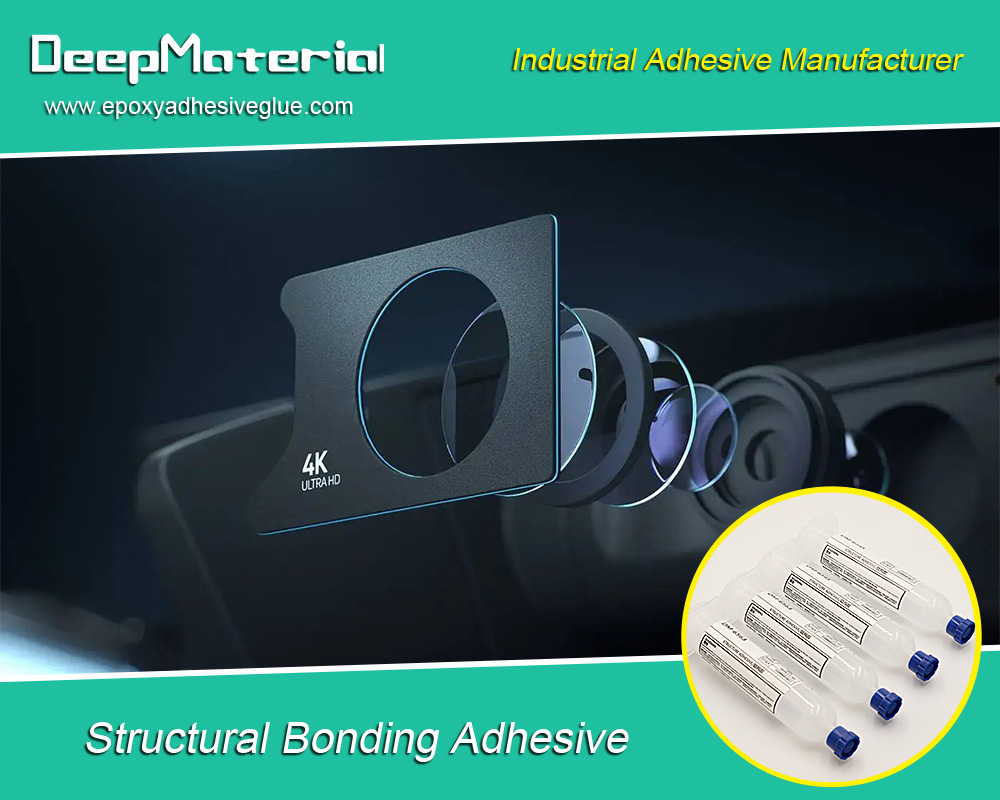
What Are Flame Retardant Adhesives for Circuit Boards?
Flame retardant adhesives for circuit boards are bonding materials formulated to resist ignition, prevent flame propagation, and maintain structural integrity when exposed to heat or fire. These adhesives are used to secure components, encapsulate circuits, or provide conformal coatings on printed circuit boards (PCBs), protecting them from electrical faults, environmental stressors, and fire hazards. Unlike standard adhesives, which may contain flammable solvents or degrade under heat, flame retardant adhesives are engineered with fire-retardant additives, low volatile organic compounds (VOCs), and thermally stable polymers to meet rigorous fire safety standards, such as UL 94 V-0, IPC-CC-830, or FMVSS 302 (Federal Motor Vehicle Safety Standard) for automotive applications.
These adhesives bond a variety of substrates, including metals, plastics, and PCB materials like FR-4, while providing insulation, vibration damping, and protection against moisture and chemicals. Their flame-retardant properties ensure that circuit boards remain safe and functional, even in high-heat or high-voltage environments.
Key Characteristics
- Fire Resistance: Prevents ignition and flame spread, meeting standards like UL 94 V-0.
- Thermal Stability: Maintains adhesion and insulation at temperatures up to 150–300°C (302–572°F).
- Electrical Insulation: High dielectric strength to prevent short circuits.
- Chemical Resistance: Withstands exposure to solvents, oils, and automotive fluids.
- Low Smoke and Toxicity: Produces minimal smoke or toxic fumes during fire exposure.
- Durability: Resists vibration, thermal cycling, and environmental degradation.
Importance in Industry
Flame retardant adhesives are critical in industries where circuit boards are exposed to fire risks, such as automotive, aerospace, and electronics. In the automotive sector, they ensure the safety of ECUs, sensors, and power electronics in high-heat zones like engine compartments or EV battery systems, while meeting regulatory requirements. By reducing fire hazards and enhancing circuit board reliability, these adhesives enable the proliferation of advanced electronics in vehicles, supporting features like autonomous driving, connectivity, and electrification.
Types of Flame Retardant Adhesives for Circuit Boards
Flame retardant adhesives for circuit boards come in various formulations, each tailored to specific applications, substrates, and performance requirements. The main types include:
Epoxy Adhesives
Epoxy-based flame retardant adhesives offer high mechanical strength, excellent electrical insulation, and thermal stability up to 200–350°C (392–662°F). They are used for bonding components, encapsulating circuits, and potting ECUs in automotive electronics, with flame-retardant additives ensuring fire safety.
Silicone Adhesives
Silicone flame retardant adhesives are flexible, heat-resistant, and inherently non-flammable, withstanding temperatures up to 300°C (572°F). They are used as conformal coatings or sealants on circuit boards, protecting against moisture, vibration, and fire in automotive and aerospace applications.
Polyurethane Adhesives
Polyurethane flame retardant adhesives provide flexibility and strong adhesion, resisting ignition up to 180°C (356°F). They are used for encapsulating or coating circuit boards in automotive infotainment systems, offering protection against environmental stressors.
Acrylic Adhesives
Acrylic flame retardant adhesives, often water-based, are used as conformal coatings, providing fire resistance up to 150°C (302°F) and good adhesion to PCB substrates. They are cost-effective for automotive interior electronics.
Polyimide Adhesives
Polyimide flame retardant adhesives excel in extreme conditions, withstanding temperatures up to 500°C (932°F). They are used in high-performance automotive applications, such as EV power electronics, where fire safety and thermal stability are critical.
Materials and Additives
- Base Polymers: Epoxies, silicones, polyurethanes, acrylics, or polyimides.
- Flame Retardants: Halogen-free additives like phosphorus, nitrogen, or mineral-based compounds (e.g., aluminum hydroxide).
- Fillers: Silica, alumina, or ceramic particles to enhance thermal stability and insulation.
- Curing Agents: Heat, UV, or moisture to initiate bonding or coating.
Properties of Flame Retardant Adhesives for Circuit Boards
The performance of flame retardant adhesives depends on several key properties:
Fire Resistance
Adhesives must meet standards like UL 94 V-0 (no flame propagation) or IPC-CC-830 (conformal coating requirements), ensuring circuit boards do not contribute to fire spread.
Thermal Stability
Maintaining adhesion and insulation at high temperatures is critical, with formulations tailored for moderate (interior electronics) to extreme (EV power electronics) conditions.
Electrical Insulation
High dielectric strength and low conductivity prevent short circuits, essential for circuit board reliability.
Mechanical Strength
Adhesives must withstand shear, tensile, and peel forces, ensuring secure bonding under vibration and thermal cycling.
Chemical Resistance
Resistance to solvents, oils, fuels, and cleaning agents ensures longevity in automotive environments.
Low Smoke and Toxicity
Minimizing smoke and toxic fume production during fire exposure is vital for passenger safety in vehicles and occupant safety in confined spaces.
Applications in the Automotive Industry
Flame retardant adhesives are critical in automotive applications, where circuit boards power safety-critical and high-performance systems.
Electronic Control Units (ECUs)
ECUs manage engine, transmission, and safety systems:
- Component Bonding: Epoxy adhesives secure chips and connectors on ECU circuit boards, with flame-retardant properties preventing fire risks.
- Encapsulation: Polyurethane adhesives pot ECUs, protecting against heat, vibration, and fire up to 180°C.
Infotainment Systems
Infotainment systems require reliable circuit boards:
- Conformal Coatings: Silicone adhesives coat circuit boards in touchscreens and navigation units, resisting fire and moisture.
- Component Sealing: Acrylic adhesives bond display modules, meeting FMVSS 302 for interior fire safety.
Electric Vehicles (EVs)
EVs introduce unique fire risks due to high-voltage systems:
- Power Electronics: Polyimide adhesives bond circuit boards in inverters and converters, withstanding temperatures up to 500°C and preventing fires.
- Battery Management Systems (BMS): Silicone adhesives coat BMS circuit boards, ensuring fire resistance and insulation.
- Charging Systems: Epoxy adhesives secure circuit boards in charging ports, resisting heat from rapid charging.
Advanced Driver Assistance Systems (ADAS)
ADAS relies on circuit boards for sensors and cameras:
- Radar and LIDAR: Silicone adhesives coat circuit boards, protecting against heat, vibration, and fire in high-heat zones.
- Camera Modules: Polyurethane adhesives bond circuit boards, ensuring fire safety and durability.
Lighting Systems
LED lighting systems use circuit boards:
- Driver Circuits: Epoxy adhesives bond LED driver circuit boards, with flame-retardant properties for safety.
- Sealing: Silicone adhesives protect lighting circuit boards from heat and moisture.
Specific Examples
- Tesla Model S: Uses flame retardant silicone adhesives to coat BMS circuit boards, enhancing EV fire safety.
- BMW i4: Employs epoxy adhesives in ECU circuit boards, meeting UL 94 V-0 standards.
- Formula E: Polyimide adhesives bond power electronics circuit boards, ensuring fire resistance in high-performance EVs.
Design Considerations
Developing flame retardant adhesives for circuit boards in automotive applications involves addressing several critical factors:
Fire Safety Compliance
Adhesives must meet standards like UL 94 V-0, IPC-CC-830, or FMVSS 302, ensuring no flame spread and low burn rates.
Thermal and Electrical Performance
Adhesives must maintain insulation and adhesion at operating temperatures, from moderate (infotainment) to extreme (EV power electronics).
Substrate Compatibility
Adhesives must bond PCB materials (e.g., FR-4), metals, and plastics, accommodating thermal expansion differences.
Application Method
Ease of application—via dispensing, spraying, or dipping—impacts manufacturing efficiency. Cure time and conditions (heat, UV, or moisture) must align with assembly processes.
Environmental Resistance
Adhesives must resist:
- Chemicals: Fuels, oils, and cleaning agents.
- Moisture: Rain or humidity in exterior applications.
- Vibration: Constant road and engine movement.
Testing and Validation
Adhesives undergo rigorous testing:
- Flammability Tests: To verify compliance with fire safety standards.
- Thermal Cycling: To simulate temperature fluctuations.
- Dielectric Tests: To confirm electrical insulation properties.
Challenges in Flame Retardant Adhesive Development
Developing flame retardant adhesives for circuit boards presents several challenges:
Balancing Fire Resistance and Performance
Flame retardants can reduce adhesive strength, flexibility, or electrical insulation. Formulating adhesives that meet fire safety standards without compromising bonding is critical.
Cost Pressures
High-performance adhesives (e.g., silicones, polyimides) are expensive. Automakers demand cost-effective solutions, requiring optimized formulations and manufacturing processes.
Environmental Impact
Some flame retardants (e.g., halogen-based) are toxic or non-recyclable, conflicting with sustainability goals. Developing eco-friendly alternatives is a priority.
Processing Complexity
Conformal coatings or encapsulants may require precise application, while heat-cured adhesives complicate manufacturing. Streamlined processes are needed for efficiency.
Long-Term Reliability
Adhesives must maintain fire resistance and bonding strength over a vehicle’s lifespan (10–15 years), resisting thermal aging and environmental degradation.
Solutions and Innovations
- Halogen-Free Retardants: Phosphorus or mineral-based additives improve safety and sustainability.
- Nanotechnology: Nanoparticles enhance fire resistance and insulation.
- Hybrid Formulations: Combine silicone and epoxy properties for versatility.
- Low-VOC Formulations: Reduce emissions during application.
Future Trends
The future of flame retardant adhesives for circuit boards is shaped by automotive and electronic advancements:
Electrification
EVs demand fire-safe adhesives for power electronics and BMS circuit boards, with higher thermal stability to prevent thermal runaway.
Autonomous Vehicles
Self-driving cars rely on circuit boards for sensors and processors. Flame retardant adhesives will ensure reliability and safety in high-heat zones.
Miniaturization
Smaller circuit boards require precise adhesive application, driving innovations in conformal coatings and encapsulants.
Sustainable Adhesives
Bio-based, recyclable, and low-VOC adhesives will align with automotive sustainability goals, reducing environmental impact.
Smart Adhesives
Adhesives with embedded sensors could monitor circuit board health or fire risk, enabling predictive maintenance.
Advanced Fire Testing
New standards for EV fire safety will drive innovation in adhesives with ultra-low flammability and smoke production.
Case Studies and Real-World Impact
- Rivian R1T: Uses flame retardant silicone adhesives to coat BMS circuit boards, enhancing EV fire safety.
- Mercedes EQS: Employs epoxy adhesives in ECU circuit boards, meeting UL 94 V-0 standards.
Aerospace Cross-Over: Automotive manufacturers adopt aerospace-grade polyimide adhesives for power electronics, improving fire resistance.
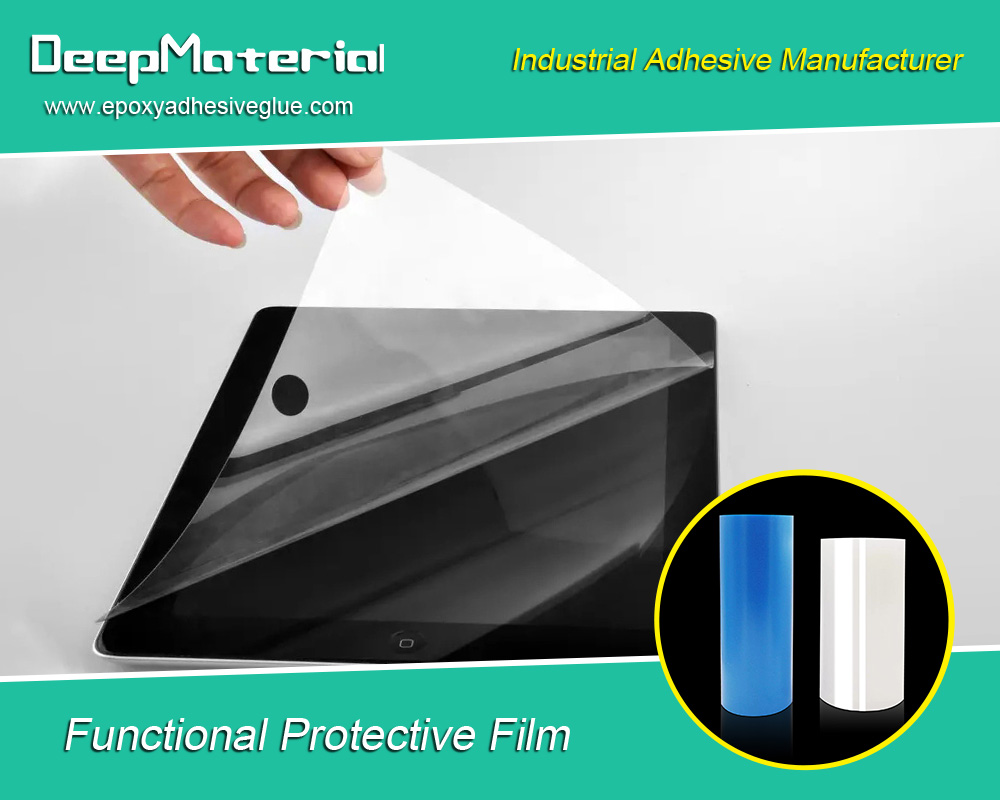
Conclusion
Flame retardant adhesives for circuit boards are essential guardians of safety and reliability in the automotive industry and beyond. From bonding ECU components to coating EV power electronics, they prevent fire hazards while ensuring circuit board performance. Designing these adhesives requires balancing fire resistance, insulation, and cost while addressing challenges like environmental impact and processing complexity. As vehicles embrace electrification, autonomy, and sustainability, flame retardant adhesives will evolve, incorporating eco-friendly materials, smarter features, and enhanced fire safety.
Next time you drive a car, use ADAS, or charge an EV, consider the flame retardant adhesives silently protecting critical circuit boards. They’re small in scale, but their impact on safety and innovation is immense.
For more about choosing the best flame retardant adhesive for circuit boards, you can pay a visit to DeepMaterial at https://www.epoxyadhesiveglue.com/category/epoxy-adhesives-glue/ for more info.