Effective Retention, Degradation and Monitoring of the Fireproof Performance of Automatic Fire Suppression Material
Effective Retention, Degradation and Monitoring of the Fireproof Performance of Automatic Fire Suppression Material
In the field of fire safety, Automatic Fire Suppression Material (AFSM), as a crucial fireproof product, the effective retention of its fireproof performance is of vital importance for ensuring the safety of people’s lives and property. Under normal storage and usage environments, having an in-depth understanding of the effective retention time of the fireproof performance of AFSM, the decay law of its performance over time, and how to monitor such changes is of great significance for its rational application and maintenance. This article will conduct a detailed discussion on these key issues.
Effective Retention Time of the Fireproof Performance of AFSM
Influence of Material Characteristics on Retention Time
The effective retention time of the fireproof performance of automatic fire suppression material primarily depends on its own chemical composition and physical structure. Different types of AFSM, such as those based on organic polymers and inorganic minerals, have different abilities to resist external factors in a normal environment due to the stability of their chemical bonds and the compactness of their molecular structures. For example, some inorganic mineral-based AFSM, due to their stable crystal structures and high-temperature resistance, can maintain their fireproof performance for a relatively long time under normal storage and usage environments, possibly up to several decades. In contrast, some organic polymer-based AFSM may have a relatively shorter effective retention time, generally ranging from several years to more than a decade, because organic molecules are vulnerable to factors such as oxidation and ultraviolet light.
Role of Storage Environment Factors
Storage environment conditions such as temperature, humidity, and light have a significant impact on the effective retention time of the fireproof performance of AFSM. In terms of temperature, both excessively high and low temperatures can change the physical and chemical properties of AFSM. In a high-temperature environment, organic components may undergo thermal decomposition and aging, and the crystal structures of inorganic components may also change, thereby reducing the fireproof performance. For example, when some AFSM is continuously exposed to a high-temperature environment above 50°C, its effective retention time will be significantly shortened. The influence of humidity on AFSM cannot be ignored either. A high-humidity environment may cause the material to absorb moisture and hydrolyze, damaging its internal structure. Especially for some AFSM with strong hydrophilicity, when the humidity exceeds 70%, its fireproof performance may decline within a relatively short period. Ultraviolet light in the light can trigger photochemical reactions in AFSM, causing the material to age and degrade, accelerating the decline of its performance. When AFSM is exposed to a strong ultraviolet environment for a long time, its effective retention time may be halved.
Influence of Usage Environment Factors
During the actual usage of AFSM, the substances it comes into contact with and the mechanical stress it endures also affect the effective retention time of its fireproof performance. If AFSM frequently comes into contact with chemically corrosive substances, such as acids and alkalis, during usage, its surface will be corroded, and its internal structure will be damaged, leading to a sharp decline in its fireproof performance and a significant reduction in the effective retention time. In terms of mechanical stress, continuous actions such as vibration, tension, and extrusion may cause cracks and deformations in AFSM, reducing its integrity and fireproof ability, and resulting in a decrease in the effective retention time.
Based on numerous research studies and practical application cases, under ideal normal storage and usage environments (temperature 20 – 25°C, humidity 40 – 60%, without strong light and chemical corrosion, etc.), the effective retention time of the fireproof performance of most high-quality AFSM can reach 10 – 20 years. However, in actual complex environments, this time will fluctuate according to specific circumstances.
Degradation of AFSM Performance over Time
Performance Degradation Caused by Changes in Chemical Structure
Over time, the chemical structure inside AFSM will gradually change. Organic components will undergo oxidation reactions, causing the molecular chains to break and cross-link, making the material harder, more brittle, and losing its original flexibility and fireproof activity. For example, organic polymers containing unsaturated double bonds are prone to oxidation of the double bonds under the action of oxygen and light, triggering a series of free radical reactions and changing the molecular structure. Inorganic components may also undergo chemical reactions. For instance, some metal oxides may undergo a hydration reaction in a humid environment, generating new compounds, changing the crystal structure and performance, and reducing the ability to block heat.
Performance Degradation Caused by Changes in Physical Structure
In terms of physical structure, AFSM will experience phenomena such as changes in porosity and particle agglomeration during long-term storage and usage. Due to factors such as thermal expansion and contraction and water evaporation, the internal pore structure of the material gradually changes. The pores become larger or the connectivity increases, which will reduce the thermal insulation performance of the material and its ability to prevent the spread of flames. Particle agglomeration will lead to uneven distribution of the material components, affecting the consistency of the fireproof performance, and the fireproof ability in some areas will be significantly weakened.
Manifestations of Performance Degradation
The performance degradation of AFSM is mainly reflected in a decrease in flame retardancy efficiency, a deterioration of thermal insulation performance, and a decline in the ability to prevent the spread of flames. A decrease in flame retardancy efficiency is manifested as the material being unable to suppress the generation and spread of flames as quickly as in its initial state during a fire, making it easier for the fire to develop. A deterioration of thermal insulation performance leads to a smaller temperature difference on both sides of the material, being unable to effectively block the transfer of heat, and causing the protected object to heat up more quickly. A decline in the ability to prevent the spread of flames means that the flame can more easily break through the barrier of the material and spread to the surroundings.
How to Monitor the Performance Changes of AFSM
Physical Performance Detection Methods
- Appearance Inspection: Regularly conduct an appearance inspection of AFSM to observe whether there are phenomena such as color change, deformation, cracks, and peeling. A color change may imply that the material has undergone chemical changes, such as oxidation and aging. Deformation and cracks will damage the integrity of the material and reduce its fireproof performance. Peeling indicates that the adhesive force between the material and the substrate has decreased.
- Density Measurement: By measuring the density change of AFSM, we can understand whether its internal structure has changed. Abnormal density changes may indicate problems such as an increase in internal pores, particle agglomeration, or component loss in the material.
- Hardness Test: Hardness is one of the important indicators reflecting the physical performance of AFSM. Use hardness testing equipment, such as a Shore durometer, to regularly detect the hardness of the material. An increase in hardness may indicate that the material is aging and becoming brittle, while a decrease in hardness may mean that the material has been chemically eroded or its internal structure has been damaged.
Chemical Performance Detection Methods
- Thermogravimetric Analysis (TGA): Thermogravimetric analysis is a commonly used chemical performance detection method. By measuring the mass change of a substance with temperature under programmed temperature control, we can understand the mass loss situation of AFSM during the heating process, determine the decomposition temperature, decomposition rate, and residual amount of organic components in the material, and thus evaluate its thermal stability and changes in chemical structure.
- Fourier Transform Infrared Spectroscopy (FT-IR): FT-IR can be used to analyze the chemical functional groups of AFSM. By comparing the infrared spectra at different times, we can detect the changes in functional groups and determine whether the material has undergone chemical reactions, aging, or contamination. For example, the appearance of new absorption peaks may indicate the formation of new compounds, and the change in the intensity of original peaks reflects the change in the content of functional groups.
- Elemental Analysis: Use an elemental analyzer to conduct elemental composition analysis of AFSM and monitor the content changes of various elements in the material. Abnormal fluctuations in elemental content may imply that the material has undergone chemical reactions. For example, the loss of some elements may be caused by corrosion or volatilization.
Fireproof Performance Testing Methods
- Small-scale Combustion Tests: For example, the Oxygen Index Test (OI) evaluates the flame retardancy performance of AFSM by determining the minimum oxygen concentration required for the material to just maintain the combustion state under specified conditions. The higher the oxygen index, the better the flame retardancy performance of the material. There are also horizontal combustion tests and vertical combustion tests, etc., to observe the combustion speed of the material in different directions and the spread of the flame, and to judge its ability to prevent the spread of flames.
- Large-scale Fire Simulation Tests: Use specialized fire test devices to simulate real fire scenes and test the actual application effect of AFSM. Observe the fireproof performance of the material in a fire, such as the thermal insulation effect and the time to prevent the flame from penetrating, and comprehensively evaluate the changes in its fireproof performance.
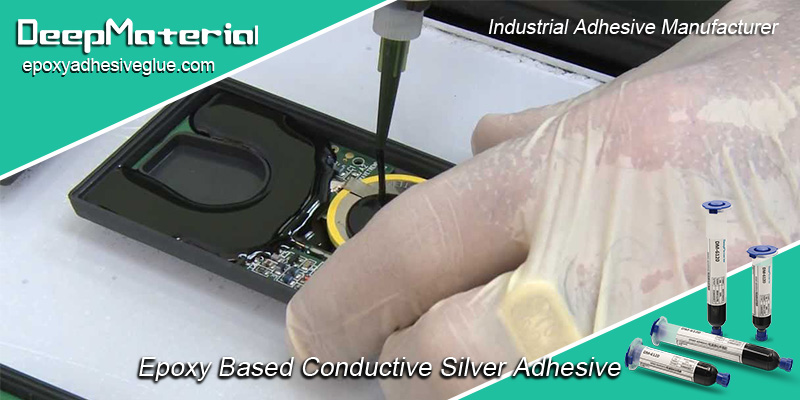
Conclusion
Under normal storage and usage environments, the effective retention time of the fireproof performance of automatic fire suppression material is comprehensively affected by various factors such as material characteristics, storage, and usage environments, generally ranging from 10 to 20 years, but there are significant differences in actual situations. Over time, AFSM will experience performance degradation due to changes in its chemical and physical structures, mainly manifested as a decrease in flame retardancy efficiency, a deterioration of thermal insulation performance, and a decline in the ability to prevent the spread of flames. In order to ensure that AFSM can play a good fireproof role at critical moments, it is necessary to comprehensively use a variety of methods such as physical performance detection, chemical performance detection, and fireproof performance testing to regularly monitor its performance changes, promptly discover problems, and take corresponding measures, such as replacing severely aged materials, to ensure fire safety. In the future, it is also necessary to conduct further in-depth research on the mechanism of performance changes of AFSM, develop more accurate and convenient monitoring technologies, and improve the fireproof reliability and service life of AFSM.
For more about choosing the best effective retention, degradation and monitoring of the fireproof performance of automatic fire suppression material, you can pay a visit to DeepMaterial at https://www.epoxyadhesiveglue.com/category/epoxy-adhesives-glue/ for more info.